3D Printing in Defense: RapidFlight’s Innovations
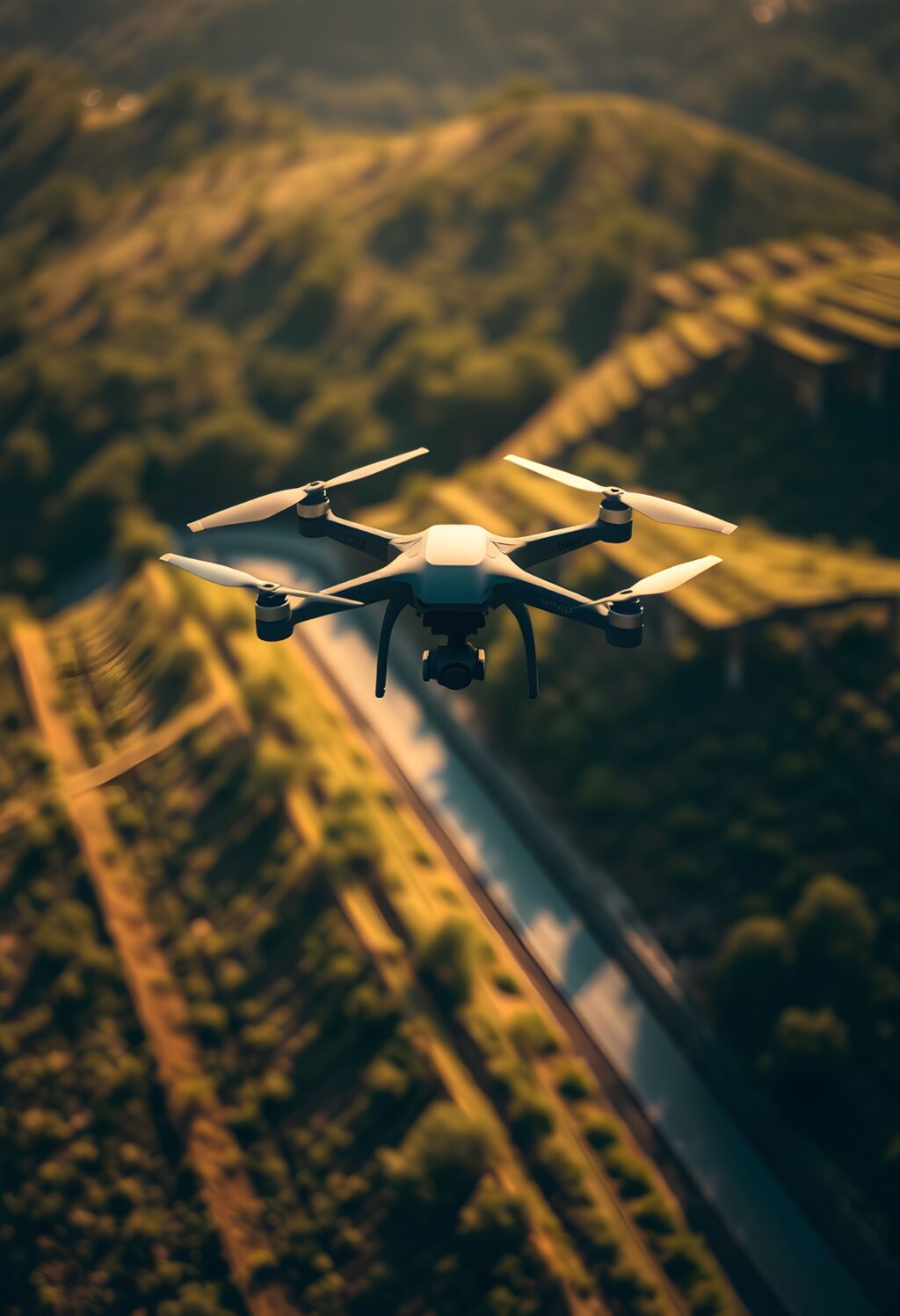
As the global defense landscape shifts rapidly due to technological advances, one American startup is disrupting traditional military manufacturing. RapidFlight, a Virginia-based aerospace firm, has introduced an innovative model that combines 3D printing with drone production to meet the growing demand for agile, mission-specific aerial systems. In a time when defense supply chains are strained and global tensions are on the rise, RapidFlight’s approach offers a compelling solution to modern military needs. By harnessing the power of additive manufacturing, the company is not only accelerating production cycles but also embracing a new paradigm: mass customization. Through the integration of advanced software and hardware, RapidFlight is delivering solutions that cater to evolving battlefield requirements in record time.
What Is RapidFlight?
Founded with the goal of transforming defense manufacturing, RapidFlight is more than just a drone company. According to CEO Esina Alic, the company views itself as a manufacturing firm that happens to build drones—not the other way around. Its operations center is based in Manassas, Virginia, and houses both design and production facilities that specialize in additive manufacturing. The company stands out in the defense space for its ability to 3D-print airframes in just 24 hours. Where traditional aerospace manufacturing can take months, RapidFlight is pushing boundaries with a digital-first approach. It uses carbon-fiber-infused thermoplastics to create drone components that are lightweight, durable, and suitable for military use. Moreover, the use of digital engineering ensures faster iteration, fewer human errors, and a more adaptable production pipeline.
3D Printing for Agility and Customization
At the heart of RapidFlight’s strategy is the concept of “mass customization”—a method that blends the benefits of mass production with the flexibility of custom design. This approach enables the company to tailor drone designs based on mission-specific requirements without sacrificing speed. For instance, if a defense client needs a drone optimized for short-range surveillance in urban environments, RapidFlight can redesign and print a unique airframe in a matter of days. Once the digital design is finalized, it is quickly fed into industrial 3D printers, which manufacture the parts using composite polymers. These parts are then assembled into functional drones using in-house fabrication and testing processes. The result is a significantly shorter production cycle, enabling militaries to adapt quickly to evolving threats and terrains.
The Role of Software in Rapid Production
RapidFlight’s edge does not lie solely in hardware—it’s also deeply rooted in software innovation. The company utilizes proprietary design tools that allow its engineers to digitally simulate various drone configurations before a single component is printed. These simulations include stress testing, aerodynamic modeling, and material optimization. This model-based engineering approach ensures that every design iteration is informed by data, enabling faster decision-making and reducing the risk of design flaws. According to CTO Matt Goyke, the emphasis on software allows the company to compress development timelines dramatically—from concept to deployment in as little as two weeks. This capability was demonstrated in late 2024 when RapidFlight recreated a version of the Iranian Shahed drone within two weeks, showcasing both its speed and strategic relevance.
Government Partnerships and Strategic Contracts
In June 2024, RapidFlight secured a contract from the U.S. Air Force’s AFWERX program to explore next-generation drone systems. This partnership is not just a milestone for RapidFlight; it’s an indicator of how seriously the Pentagon is taking additive manufacturing in national defense. The company’s solutions are being tested in a variety of military exercises, including rapid deployment scenarios and operations in contested environments. These field trials aim to evaluate not just the performance of the drones, but also the scalability of RapidFlight’s manufacturing process. By embedding printers in modular, deployable units—sometimes referred to as “digital foundries”—the company envisions forward-operating bases being capable of printing their own drone fleets in real-time.
Reproducing Threat Models: The Shahed Drone Case
One of RapidFlight’s most impressive feats was its reproduction of the Shahed-136, a loitering munition drone used by Russia in Ukraine and originally developed by Iran. This replication wasn’t for deployment but rather to help U.S. forces better understand how to defend against such systems. RapidFlight reverse-engineered the airframe and reprinted it in-house using its proprietary methods. The entire process took less than 14 days from request to first flight. This ability to reproduce and simulate adversary drones offers a valuable tactical edge, allowing the U.S. military to test countermeasures in realistic settings. Additionally, this capability serves as a proof-of-concept for rapid prototyping in a combat context, further validating the company’s mass customization model.
The Advantages of Additive Manufacturing in Defense
Traditional defense manufacturing has long been plagued by delays, costs, and rigidity. Parts often require machining, tooling, and labor-intensive processes that slow production and limit flexibility. In contrast, 3D printing—or additive manufacturing—builds objects layer by layer from digital files, drastically reducing the time needed to move from design to production. For defense applications, this means drones can be modified, printed, and fielded with remarkable agility. RapidFlight’s use of thermoplastics reinforced with carbon fiber offers strength and durability while remaining light enough for aerial use. Additionally, digital inventory management eliminates the need for large warehousing of parts. Instead of storing thousands of drone wings, for instance, the company simply stores the design file and prints the part on demand. This approach is especially beneficial for expeditionary forces and remote bases where supply lines are vulnerable or disrupted.
Challenges and Limitations
Despite its promise, RapidFlight’s model is not without challenges. Additive manufacturing in the aerospace domain must meet strict quality assurance and regulatory standards. While printing a component quickly is feasible, ensuring that it meets the necessary safety and performance criteria is more complex. Furthermore, materials used in 3D printing must be carefully selected and tested for temperature resistance, UV degradation, and structural integrity under load. The company addresses these challenges through rigorous testing and validation protocols, both in simulations and in the field. Another concern is cybersecurity. As production becomes more digital, the risks of file corruption, hacking, or intellectual property theft increase. RapidFlight has invested in secure design environments and encrypted data transfers to safeguard its IP and the sensitive nature of defense work.
Expanding into the Global Market
With the success of its U.S. operations, RapidFlight is looking to scale globally. The company is in discussions with allied nations about setting up localized digital foundries that can print drones on-site using licensed technology. This model not only reduces dependence on centralized production hubs but also allows partner nations to respond more independently to regional security needs. As military alliances shift towards joint operations and shared technology, RapidFlight’s flexible model aligns well with emerging defense collaboration strategies. The company’s interest in scalable, mobile production units could transform how future conflicts are supplied and supported, potentially enabling “on-the-fly” adjustments to tactics using locally printed drones.
Future Outlook: The Road Ahead
Looking forward, RapidFlight’s roadmap includes the integration of AI in design processes, machine learning for automated flight optimization, and expanded drone form factors. While its current focus is on Group 2 and 3 UAVs—typically weighing between 20 and 55 pounds—it is exploring lightweight loitering munitions and autonomous swarm capabilities. The company also plans to increase the automation of its manufacturing floor, aiming for a future where drones are designed, printed, tested, and shipped with minimal human intervention. These advancements could mark a paradigm shift not just in defense, but in how industrial products are conceived and delivered across sectors.
In a defense environment increasingly defined by speed, adaptability, and decentralized operations, RapidFlight’s innovations in 3D printing are setting a new standard. By fusing advanced materials, digital design, and additive manufacturing, the company is redefining what’s possible in military drone production. From faster turnaround times to mission-specific configurations, RapidFlight embodies the future of agile defense manufacturing. As geopolitical tensions rise and the need for tactical innovation grows, their approach offers a blueprint for military readiness in the 21st century.
Feel free to check out our other website at : https://synergypublish.com