What is 3D Printing: A Comprehensive Look
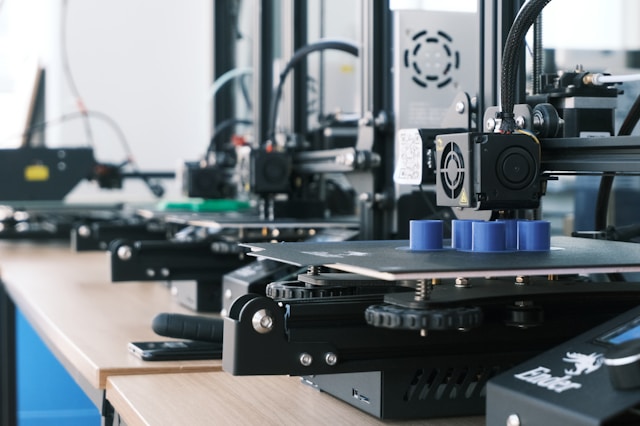
3D printing, also known as additive manufacturing, is a transformative technology that creates three-dimensional objects by building them up layer by layer from a digital model. Here’s a comprehensive look at what 3D printing entails:
Basic Principles
Additive Manufacturing:
Unlike traditional manufacturing methods that often involve subtracting material (like cutting or milling), 3D printing builds objects by adding material. This layer-by-layer approach allows for the creation of complex geometries that would be difficult or impossible with other methods.
Digital Model:
The process starts with a digital 3D model, often created using Computer-Aided Design (CAD) software. This model is then sliced into thin horizontal layers, which guide the printer in building up the object.
Common Technologies
Fused Deposition Modeling (FDM):
This is one of the most common 3D printing methods, particularly for consumer-grade printers. It works by extruding a thermoplastic filament through a heated nozzle to build up layers.
Stereolithography (SLA):
SLA uses a laser to cure a liquid resin in a vat, layer by layer. The laser solidifies the resin based on the 3D model, allowing for high-resolution and detailed prints.
Selective Laser Sintering (SLS):
SLS involves using a laser to sinter powdered material, such as nylon or metal, into solid structures. It’s suitable for creating durable and complex parts.
Digital Light Processing (DLP):
Similar to SLA, DLP uses a projector to cure resin. It typically has a faster print time due to its use of a digital light source.
Direct Metal Laser Sintering (DMLS):
DMLS is used for printing metal parts. It uses a laser to fuse metal powder into solid metal components, often used in aerospace and automotive industries.
PolyJet Printing:
This method involves spraying tiny droplets of photopolymer resin onto a build platform and curing them with UV light. It’s known for its ability to print multi-material and high-resolution objects.
Materials Used
Plastics:
Common materials include thermoplastics like PLA (Polylactic Acid), ABS (Acrylonitrile Butadiene Styrene), and PETG (Polyethylene Terephthalate Glycol). Each has its own properties in terms of strength, flexibility, and ease of use.
Resins:
Used primarily in SLA and DLP printing, resins come in various types, including standard, flexible, and castable resins, each offering different properties.
Metals:
Materials like titanium, aluminum, and stainless steel are used in industrial 3D printing for high-strength applications.
Composites:
These are materials that combine plastics with other substances, like carbon fiber or glass fibers, to enhance properties such as strength or rigidity.
Ceramics and Bio-materials:
Some advanced 3D printers can work with ceramics and bio-materials for specialized applications.
Applications
Prototyping:
Rapid prototyping is one of the most common uses. Designers and engineers can quickly create and test prototypes, iterating designs more efficiently than with traditional methods.
Manufacturing:
3D printing is increasingly used for producing end-use parts and products, especially in industries like aerospace, automotive, and healthcare.
Medical Field:
In medicine, 3D printing is used to create custom prosthetics, implants, and even bioprint tissues and organs.
Architecture and Construction:
Models and even some components of buildings can be created using 3D printing, offering more flexibility in design and construction techniques.
Consumer Products:
From custom jewelry to personalized gadgets, 3D printing allows for the production of unique, tailored products.
Advantages
Customization:
3D printing allows for high levels of customization and personalization, which is valuable in many fields, including healthcare and consumer goods.
Complex Geometries:
The layer-by-layer approach can produce complex shapes and intricate details that are difficult to achieve with traditional manufacturing.
Material Efficiency:
Additive manufacturing often results in less waste compared to subtractive methods, as material is added only where needed.
Rapid Production:
The ability to quickly produce prototypes and final products can significantly shorten development cycles.
Challenges
Material Limitations:
While the range of materials is growing, not all materials are available for all types of 3D printers, and some may not match the properties of traditional materials.
Print Speed:
While 3D printing is evolving, the process can still be slow, particularly for large or complex objects.
Surface Finish:
Depending on the technology used, the surface finish might require additional post-processing to achieve a smooth or polished appearance.
Cost:
High-end 3D printers and materials can be expensive, making the technology more accessible for industrial applications than for personal use.
Future Trends
Advancements in Materials:
Development of new materials, including better metals, composites, and even bio-materials, will expand the possibilities of 3D printing.
Increased Speed and Precision:
Future innovations aim to improve the speed and accuracy of 3D printing, making it more practical for a wider range of applications.
Integration with Other Technologies:
Combining 3D printing with technologies like AI, robotics, and the Internet of Things (IoT) could enhance automation and capabilities in manufacturing and design.
Sustainability:
Efforts are being made to improve the environmental impact of 3D printing, such as developing recyclable materials and more energy-efficient processes.
3D printing is a rapidly evolving field with the potential to revolutionize various industries. As technology advances, it’s likely to become even more integrated into both industrial and everyday applications.