Transforming Manufacturing: 3D Printing for the Factory Floor
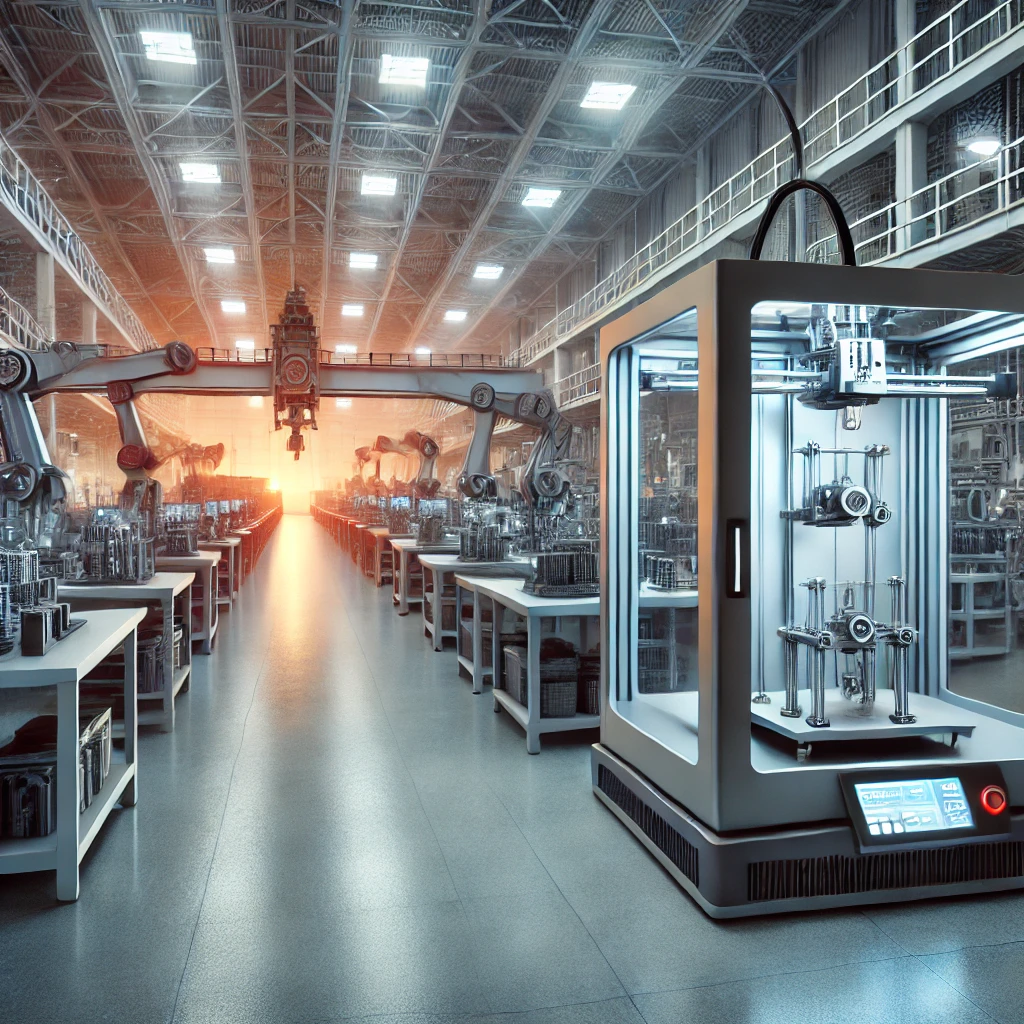
In the fast-paced world of manufacturing, few technologies have been as transformative as 3D printing. Known technically as additive manufacturing, this process builds objects layer by layer from digital designs, enabling unprecedented innovation, speed, and efficiency. Originally a tool for rapid prototyping, 3D printing has evolved to become an integral part of factory floors worldwide.
As of 2024, advancements in materials, machinery, and software have propelled 3D printing into mainstream manufacturing. Its ability to address challenges like material waste, customization, and supply chain disruptions has positioned it as a vital tool for industries ranging from automotive and aerospace to healthcare and consumer goods.
This comprehensive article will explore the evolution of 3D printing in manufacturing, the latest trends driving its growth, its numerous benefits, real-world applications, and the challenges it faces. Additionally, we will delve into its future potential and why embracing this transformative technology is essential for manufacturers aiming to stay competitive.
The Evolution of 3D Printing in Manufacturing
The journey of 3D printing began in the early 1980s when Chuck Hull developed stereolithography (SLA), a technique for creating three-dimensional objects using ultraviolet light to harden liquid resin. This marked the birth of additive manufacturing, which offered an innovative way to create complex designs with minimal waste.
Throughout the 1990s, the development of fused deposition modeling (FDM) and selective laser sintering (SLS) expanded the scope of 3D printing. These advancements allowed for the creation of more durable and intricate components, though the technology remained limited to prototyping due to high costs and material limitations.
The early 2000s saw a shift as researchers began exploring the potential of 3D printing for full-scale manufacturing. Metal 3D printing emerged as a game-changer, enabling industries like aerospace and automotive to produce high-performance components with precision and efficiency.
By the 2010s, industries recognized the potential of 3D printing to revolutionize production. Advancements in materials, such as carbon fiber-reinforced polymers and bio-based plastics, made it possible to create end-use products. The affordability of desktop 3D printers also popularized the technology among small businesses and hobbyists.
In response to the global disruptions of the early 2020s, manufacturers turned to 3D printing to localize production and mitigate supply chain vulnerabilities. This approach proved effective in maintaining operations during crises, demonstrating the technology’s adaptability and resilience.
As of 2024, 3D printing is no longer a niche tool but a critical component of Industry 4.0. Its integration with artificial intelligence, robotics, and IoT has elevated manufacturing to new heights, paving the way for smarter, more efficient production systems.
Current Trends and Technologies in 2024
The ongoing evolution of 3D printing is shaped by several key trends and innovations:
a. Advanced Materials
In 2024, the development of materials tailored for 3D printing has opened new possibilities. High-strength polymers, metal alloys, and even ceramics are now commonly used, enabling the production of durable and lightweight components. Bio-based and recycled materials are also gaining traction, aligning with sustainability goals.
b. AI-Driven Design
Artificial intelligence has become an invaluable partner in additive manufacturing. AI-powered software analyzes design parameters, optimizes structures for strength and material efficiency, and generates innovative geometries that were previously impossible with traditional methods.
c. Multi-Material Printing
The ability to print with multiple materials simultaneously is revolutionizing product functionality. Manufacturers can create components with varying properties—such as flexibility, conductivity, and strength—in a single production process, enhancing performance and reducing assembly requirements.
d. Hybrid Manufacturing Systems
Hybrid manufacturing systems combine the strengths of traditional manufacturing methods with 3D printing. This approach allows factories to integrate additive manufacturing seamlessly into their existing workflows, maximizing efficiency and versatility.
e. Large-Scale 3D Printers
Industrial-scale 3D printers are addressing the growing demand for larger components. These machines are particularly valuable in industries like aerospace, construction, and energy, where they can produce complex, high-performance parts in record time.
f. Sustainability Initiatives
Sustainability remains a driving force behind the adoption of 3D printing. By minimizing waste, enabling the use of recycled materials, and supporting localized production, additive manufacturing helps reduce the environmental impact of traditional production methods.
These trends underscore how 3D printing is not only a technological advancement but a catalyst for innovation and sustainability in modern manufacturing.
Benefits of 3D Printing on the Factory Floor
a. Cost Efficiency
One of the primary advantages of 3D printing is its ability to reduce costs. By eliminating the need for expensive tooling and minimizing material waste, manufacturers can achieve significant savings. On-demand production also reduces inventory costs, as parts can be created as needed, avoiding overproduction.
b. Customization
Mass customization has become a reality thanks to 3D printing. Unlike traditional manufacturing, where customization incurs high costs, additive manufacturing allows for tailored designs without impacting efficiency. This capability is particularly valuable in industries like healthcare and consumer goods.
c. Accelerated Production
The speed of 3D printing shortens development cycles, allowing manufacturers to bring products to market faster. Prototyping, testing, and refinement can be completed in days instead of weeks, giving companies a competitive edge.
d. Lightweight Structures
In industries like aerospace and automotive, reducing weight is crucial for enhancing performance and efficiency. 3D printing enables the creation of lightweight structures with complex geometries, offering a perfect balance of strength and functionality.
e. Enhanced Innovation
The flexibility of 3D printing fosters innovation by enabling designers to experiment with unconventional shapes and structures. This creative freedom results in products that are not only functional but also visually unique and optimized for their intended purposes.
f. Sustainability
3D printing contributes to sustainable manufacturing by reducing waste and enabling the use of eco-friendly materials. Localized production further reduces the carbon footprint associated with transportation and logistics.
These benefits highlight why 3D printing is becoming an indispensable tool for manufacturers seeking to stay competitive in a rapidly changing industry.
Real-World Applications
a. Automotive Industry
In the automotive sector, 3D printing is revolutionizing how vehicles are designed and manufactured. Companies like BMW and Ford use the technology to produce lightweight components, improve fuel efficiency, and create custom parts for electric vehicles. Prototyping is also faster, enabling quicker iterations on new designs.
b. Aerospace and Defense
The aerospace and defense industries rely on 3D printing for its ability to produce high-performance components with precision. Complex parts, such as jet engine components and satellite structures, can be manufactured efficiently, reducing weight and material usage.
c. Healthcare
Healthcare is one of the most transformative sectors for 3D printing. Personalized prosthetics, implants, and surgical tools are now produced with unmatched precision. Additionally, bioprinting, which involves creating tissues and organs using living cells, holds immense potential for regenerative medicine.
d. Consumer Goods
3D printing is enhancing the consumer goods industry by enabling mass customization. Companies are creating tailored products, such as eyewear, footwear, and jewelry, that cater to individual preferences. This approach not only improves customer satisfaction but also reduces waste from overproduction.
These applications demonstrate the versatility and transformative potential of 3D printing across various industries.
Challenges and Limitations
Despite its many advantages, 3D printing faces several challenges that manufacturers must overcome:
- Material Costs: While the technology has become more affordable, high-quality materials for 3D printing remain expensive.
- Production Speed: Additive manufacturing is faster for prototyping but can be slower than traditional methods for large-scale production.
- Skill Requirements: Operating advanced 3D printers requires specialized knowledge, necessitating workforce training.
- Quality Assurance: Ensuring consistent quality across large-scale production remains a challenge, especially in industries with stringent regulatory requirements.
- Intellectual Property Concerns: The digital nature of 3D printing raises concerns about intellectual property theft and unauthorized reproduction of designs.
Addressing these challenges is essential for the widespread adoption of 3D printing in manufacturing.
Future Prospects
The future of 3D printing is filled with exciting possibilities. Emerging technologies like multi-material printing and bioprinting are expected to unlock new applications in fields such as healthcare, construction, and energy. Additionally, research into faster production methods aims to overcome current limitations in speed.
By 2030, 3D printing could become a central pillar of Industry 5.0, emphasizing human-machine collaboration to create efficient, sustainable, and innovative production systems. Fully automated factories equipped with AI and robotics will integrate additive manufacturing seamlessly, revolutionizing how products are made.
3D printing has come a long way from its early days as a prototyping tool. As of 2024, it is reshaping manufacturing, offering unmatched benefits in customization, efficiency, and sustainability. While challenges remain, ongoing advancements promise to unlock even greater potential for this transformative technology.
For manufacturers looking to stay ahead in a competitive landscape, embracing 3D printing is not just an option—it’s a necessity. By adopting this revolutionary approach, companies can position themselves as leaders in the next wave of industrial innovation.