How to 3D Print Custom Enclosures for Your Electronics Projects
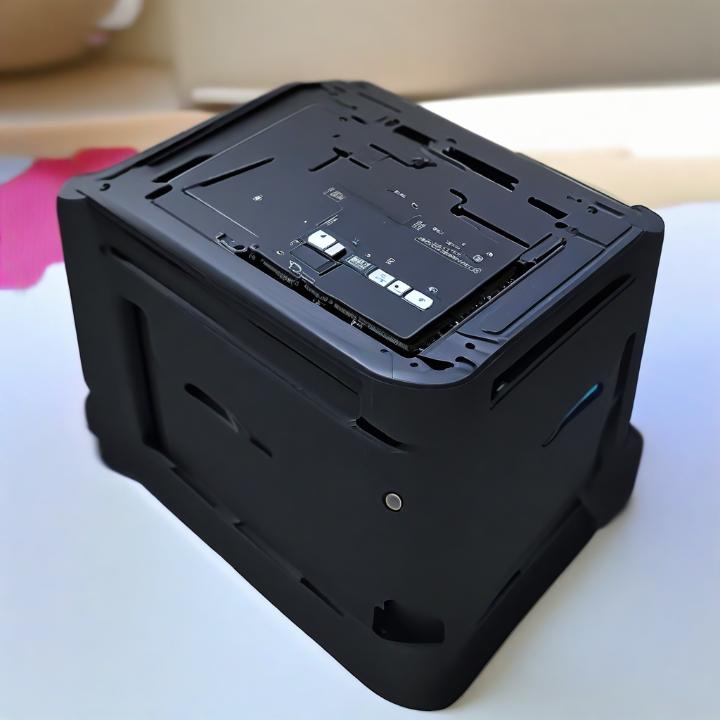
Learn how to design and 3D print custom enclosures for your electronics projects. Master advanced 3DP techniques to create durable, functional, and aesthetically pleasing protective cases for your DIY builds.
3D Print Custom Enclosures
Creating custom enclosures for your electronics projects can elevate both the functionality and aesthetics of your build. Whether you’re designing a case for a Raspberry Pi, Arduino, or any other electronic device, 3D printing allows you to tailor the enclosure exactly to your requirements. This guide will cover in-depth how to design, prepare, and print enclosures that not only protect your components but also improve usability and longevity.
Step 1: Planning the Design
Before opening your CAD software, it’s crucial to thoroughly plan the design of your enclosure. This ensures that all components fit properly and that the case performs its intended functions.
A. Identify Components and Their Layout
- Measure your electronics: Begin by measuring all components that need to be housed in the enclosure. Use precise calipers to measure circuit boards, sensors, power supplies, displays, and connectors.
- Consider arrangement and stacking: For multi-board setups like Raspberry Pi with HATs or shields, ensure there’s enough space vertically. Plan the orientation of components to minimize cable clutter and interference.
- Cooling requirements: Electronic devices like Raspberry Pi and other microcontrollers can generate heat. Plan to include ventilation holes, heat sinks, or even fans if necessary to prevent overheating.
B. Define Enclosure Features
- Access to I/O Ports: Ensure that USB, HDMI, power, Ethernet, and other connectors have adequate space for easy access. Design precise openings for these ports.
- Mounting holes: If your project requires mounting to a surface, add holes for screws or brackets.
- Aesthetic considerations: Decide if the enclosure should have smooth surfaces or decorative elements, such as a brand logo or etched designs.
C. Choose a Form Factor
- Determine whether your enclosure will be slim, boxy, or modular. Depending on where the enclosure will be placed (wall-mounted, desktop, or portable), you may want to vary its dimensions.
Step 2: Designing the Enclosure Using CAD Software
Once you’ve mapped out the layout and features, you can begin the design process in CAD software. For advanced control, software like Fusion 360 or SolidWorks is ideal, while Tinkercad is more beginner-friendly.
A. Designing the Outer Shell
- Create the enclosure walls: Start by designing the external shell of the enclosure. Keep the wall thickness around 2-3 mm for durability while minimizing excess material.
- Design for fit: Leave enough clearance (usually around 0.5 mm) between parts of the enclosure and the components it will house. This ensures a proper fit without stressing the electronics.
B. Add Component Mounts and Stand-offs
- Stand-offs: Design stand-offs or small pillars to hold the circuit board in place. These stand-offs should have mounting holes that align with the board’s mounting points.
- Component-specific mounts: For parts like screens, buttons, or sensors, create recesses or brackets to hold them securely in place. Use screws or press-fit slots to attach them.
C. Openings and Hinges
- Port openings: Accurately measure and position openings for USB, Ethernet, HDMI, and other ports. Be mindful of cable clearance and connector accessibility.
- Hinges or Snap-fit mechanisms: If your enclosure needs to open and close for maintenance or access, design hinges or a snap-fit locking mechanism to provide easy access.
Step 3: Preparing for 3D Printing
Now that your model is complete, it’s time to slice it and prepare for printing. The settings you choose here will determine the strength, quality, and functionality of your enclosure.
A. Import the Design into Slicing Software
- STL format: Export your design from the CAD program as an STL file and load it into slicing software such as Cura, PrusaSlicer, or Simplify3D.
B. Optimizing Print Settings
- Layer Height: A layer height of 0.2 mm is ideal for enclosures, offering a balance between speed and detail. For more intricate designs, reduce this to 0.1 mm.
- Infill Density: Use a 15-25% infill for a strong but lightweight print. For more structural parts like mounts or hinges, consider increasing the infill to 30-40%.
- Supports: Enable supports for overhangs, especially around complex cutouts and hinge mechanisms.
C. Filament Selection
- PLA: Easy to print and suitable for most indoor enclosures.
- PETG: More durable and heat-resistant, ideal for enclosures that will be exposed to higher temperatures.
- ABS: Provides excellent heat resistance and impact strength but requires a heated bed and controlled printing environment.
Step 4: Post-Processing Your 3D-Printed Enclosure
After printing, the enclosure may require some post-processing to remove supports and refine the finish.
A. Removing Supports and Sanding
- Carefully remove support structures with pliers or a deburring tool. Sand down any rough edges, especially around cutouts for ports and buttons.
B. Assembly and Test Fit
- Before final assembly, test the fit of all components inside the enclosure. Make sure that all mounting holes align and that ports are accessible without obstruction.
- If necessary, make minor adjustments by sanding or reprinting sections.
C. Painting and Coating (Optional)
- For a professional finish, you can paint the enclosure or apply a protective coat. Acrylic spray paints or polyurethane coatings work well on 3D-printed plastics.
Step 5: Assembling the Enclosure
With the printed enclosure ready, it’s time to install your electronics and finalize the project.
A. Install the Components
- Secure your components to the stand-offs or mounts inside the enclosure. Use M2 or M3 screws to hold circuit boards in place.
- Attach any external accessories like buttons, displays, or sensors as per the design.
B. Seal the Enclosure
- Once all components are in place, close the enclosure. If you’ve designed a snap-fit case, it should snap together securely. For screw-fastened enclosures, ensure all screws are tightened to avoid any movement.
Mastering 3DP techniques for creating custom enclosures allows you to protect and enhance your electronics projects. With thoughtful design, precise planning, and optimal print settings, you can create enclosures that not only house your components but also improve their functionality and lifespan. Whether you’re building a simple Raspberry Pi case or an advanced multi-component system, 3D printing gives you the flexibility to create custom solutions tailored to your needs.