10 Groundbreaking 3D Printing Applications in Healthcare
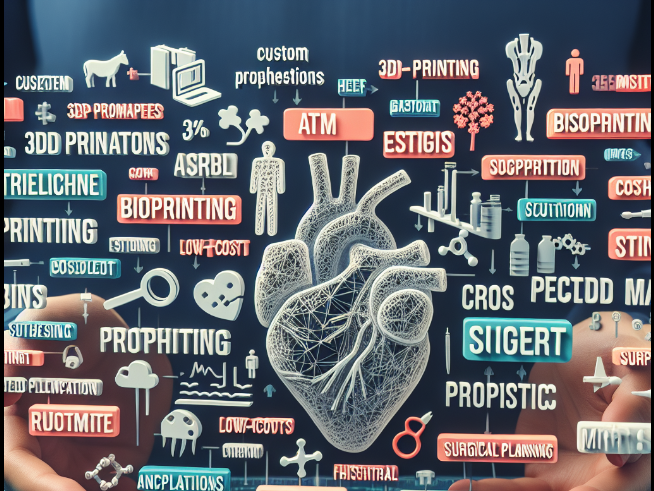
Explore how 3D printing is transforming healthcare—from prosthetics to bioprinting organs—and learn about real-world applications and success stories.
Transforming Healthcare with 3D Printing
In the field of healthcare, innovation has consistently paved the way for longer, healthier, and more fulfilling lives. Over the past decade, 3D printing technology has become one of the most transformative tools in modern medicine , fundamentally altering how treatments and devices are developed and delivered to patients. From affordable prosthetics to bioprinted organs, the possibilities seem limitless.
3D printing, also known as additive manufacturing , produces three-dimensional objects layer by layer using materials such as plastics, titanium, ceramics, and even biological materials like living cells (bioinks). Its ability to create highly customized, patient-specific solutions has played a pivotal role in solving problems previously considered insurmountable. For example, 3D printing reduces wait times for organ transplants by creating bioprinted tissue samples and prosthetics for people in underserved communities who previously had no access to such solutions.
Moreover, the potential of 3D printing in healthcare is colossal. According to Allied Market Research, the global 3D printing healthcare market is projected to reach $5.8 billion by 2030 , growing at a staggering rate of 18.2% per year. As this technology grows, so does its ability to disrupt healthcare industries around the world. This article highlights 10 groundbreaking applications of 3D printing in healthcare , focusing on real-world case studies and industry success stories.
1. Personalized Prosthetics: Tailored, Affordable Solutions
For decades, prosthetic development was limited by rigid molds, expensive materials, and labor-intensive processes. However, the introduction of 3D printing has redefined prosthetics , making them more affordable, customizable, and widely accessible. Personalization is the key to success here, as prosthetics produced with 3D printing can be designed specifically to match the patient’s unique anatomy, offering enhanced comfort and functionality.
The Accessibility Revolution
Traditional prosthetic limbs are often prohibitively expensive, costing between $5,000 and $50,000 , and manufacturing custom prosthetics takes weeks or even months. In contrast, 3D printing has driven down production costs to as little as $50–$100 per prosthetic , drastically reducing both price and turnaround time. This affordability is especially impactful in developing nations where limited resources previously denied countless individuals access to prosthetics.
Case Study: The Hero Arm by Open Bionics
Open Bionics, a UK-based company, is a powerful example of how 3D printing is transforming prosthetics. Their flagship product, the Hero Arm , is an advanced bionic arm targeted at those living with limb differences. The Hero Arm is not only functional but also personalized and accessible.
- Affordable Innovation : Each Hero Arm is up to 40% cheaper than traditional bionic prosthetics, with prices starting at around $3,000. This affordability is achieved through 3D printing, which reduces production costs without compromising quality.
- Customization : Users can choose from a range of designs, including arms inspired by Iron Man and Star Wars, empowering children and adults to express their individuality. The arms include multi-grip functionality and a lightweight build, making them easy to use.
- Impact on Lives : Take Tilly Lockey, a teenager from the UK who lost her hands during childhood. After receiving the Hero Arm, Tilly regained independence, allowing her to perform tasks as varied as cooking and playing musical instruments. This success story shows how technology can profoundly enhance quality of life.
Global Scaling
Beyond Europe, similar success is being replicated worldwide. Nonprofits such as e-NABLE use community networks of 3D printers to create prosthetic hands for children in need, offering life-altering solutions for nearly no cost.
2. Bioprinting Human Tissues: Closing the Gap in Organ Transplants
Bioprinting , a specialized branch of 3D printing, uses living cells and biomaterials (known as bioinks ) to produce tissue-like structures. While researchers are still years away from creating fully functional organs, the progress made so far in bioprinting is nothing short of revolutionary.
Addressing the Organ Donor Crisis
Over 17 people die every day in the U.S. alone waiting for an organ transplant. Bioprinting offers hope to thousands of patients by creating lab-grown tissues and organ models for research, drug testing, and even future transplants. Researchers have made strides in creating kidney prototypes, functional liver tissue, and cardiac patches that can address specific medical needs.
Case Study: Wake Forest’s 3D-Printed Skin
The Wake Forest Institute for Regenerative Medicine (WFIRM) is a pioneer in bioprinting. By creating 3D-printed skin grafts , they aim to treat burn victims more effectively.
- Technology in Action : Scientists create bioinks using cells harvested directly from the patient to print sheets of skin that perfectly match the wound’s size and shape. This minimizes the risk of rejection while promoting faster healing.
- Real-Life Applications : One notable project involves printing skin directly onto burn sites to help soldiers injured in combat. The ability to deploy this technology in war zones could save countless lives in emergencies.
- Challenges and Progress : While full-scale deployment isn’t yet a reality, early trials have shown immense promise in reducing healing times and improving patient comfort.
The Future of Bioprinting
Efforts to scale bioprinting are intensifying. Researchers at Tel Aviv University recently created a 3D-printed heart prototype that includes living tissues, blood vessels, and chambers. Although too small for human use, it demonstrates the potential for larger, functional organs in the future.
3. 3D-Printed Surgical Models: Enhancing Precision in Complex Surgeries
Surgical procedures often require surgeons to visualize and plan for unique anatomical challenges. With 3D-printed surgical models , healthcare professionals can prepare for operations with unparalleled accuracy, leading to better outcomes and shorter operating times.
Case Study: Boston Children’s Hospital and Heart Models
Boston Children’s Hospital is a leader in using 3D-printed heart models to prepare for pediatric surgeries. These models are created using MRI or CT scans to replicate the patient’s heart structure down to the smallest details, giving surgeons a tangible tool to study before performing the procedure.
- Congenital Heart Defects : One child with a rare and complex congenital heart defect recently benefitted from this approach. The surgical team was able to rehearse the surgery using the 3D-printed model, which allowed them to perfect their approach before stepping into the operating room.
- Reduced Operating Times : As a result, the surgery’s duration dropped by 30% , which significantly reduced stress on the patient’s body and lowered the risks of complications.
- Life-Saving Impact : The child recovered faster than expected, paving the way for hospitals around the world to adopt similar methods.
Wider Applications
Beyond cardiac surgeries, hospitals are now using 3D-printed surgical models for brain surgeries, orthopedic reconstructions, and even separating conjoined twins. These realistic models allow surgeons to experiment with different techniques and minimize risks.
4. Orthopedic Implants: Precision-Driven Solutions
The use of 3D printing in orthopedic implants has emerged as one of the most transformative advancements in modern healthcare. When it comes to joint replacements, bone reconstruction, or implants used in complex fractures, traditional production methods often fall short of meeting the personalized needs of individual patients. This is where 3D printing steps in, offering customized, exact-fit solutions that ensure higher comfort, durability, and surgical success rates.
Custom Joint Replacements
One of the most common applications of 3D printing in orthopedics is the production of patient-specific joint replacements. These implants are tailored to the individual’s anatomical structure using medical imaging data such as CT scans and MRI results . This reduces the risks associated with poorly-fitted implants, such as discomfort, joint instability, and reduced mobility. For patients requiring hip or knee replacements, customized implants have shown to improve postoperative recovery while reducing the risk of complications.
Furthermore, materials like titanium alloys —commonly used in 3D-printed implants—offer exceptional strength and biocompatibility. The porous nature of 3D-printed titanium implants also enhances the integration with the patient’s natural bone tissue, encouraging faster recovery and reducing the chances of implant rejection.
Case Study: Oxford’s 3D-Printed Knee Replacement
One of the most famous applications of 3D printing in orthopedics occurred at the Nuffield Orthopedic Centre in Oxford, UK. A 67-year-old woman suffering from severe osteoarthritis underwent knee replacement surgery using custom 3D-printed titanium parts that perfectly matched her unique anatomy.
- Design Process : The medical team used MRI scans to map the patient’s knee structure in precise detail. This data was fed into a 3D printer, which crafted a knee implant that mimicked the natural contours of her joint.
- Surgical Advantages : The implant’s tailored fit minimized the need for extensive bone removal during surgery, making the operation far less invasive than traditional methods.
- Results : Post-surgery, the patient reported higher mobility and reduced pain within weeks. The procedure proved how 3D printing could enhance accuracy and reduce rehabilitation periods in orthopedic surgery.
Scalable Solutions for Global Markets
Another milestone in orthopedic 3D printing is its potential for scaling cost-effective solutions. In India, surgeons use cost-efficient 3D-printed orthopedic devices for patients who cannot afford traditional implants. These low-cost alternatives, often powered by local 3D printing labs, have democratized access to life-changing surgeries across rural and economically underprivileged regions.
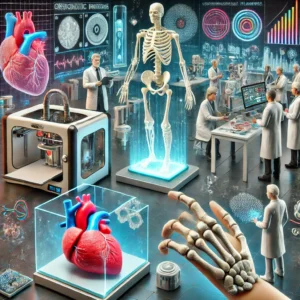
5. Revolutionizing Surgical Planning with 3D Models
Surgical planning has always been a critical step in performing complex operations. While imaging tools such as CT or MRI scans have aided surgeons in visualizing patient anatomies, they have limitations when it comes to real-world application. Enter 3D-printed anatomical models —physical replicas of a patient’s unique inner structures created with incredible precision.
Why 3D-Printed Models Matter
These models allow surgeons to rehearse procedures, test different strategies, and identify potential challenges before performing the actual surgery. This leads to better preparation, faster surgeries, fewer errors, and improved outcomes. For particularly high-risk surgeries, such as those involving the heart, brain, or spinal cord, 3D-printed models have proven invaluable.
Case Study: Separating Conjoined Twins
In 2017, surgeons at Texas Children’s Hospital demonstrated the power of surgical models when they successfully performed the separation of conjoined twins. The twins were conjoined at the chest and abdomen, sharing a liver and several other crucial organs—a highly complex case requiring months of preparation.
- Model Creation : Using precise imaging data, a 3D-printed replica of the twins’ conjoined anatomy was created. The surgeons used this to simulate the operation multiple times, testing different approaches for organ separation and vascular system reconstruction.
- Reduced Risks : The detailed rehearsals identified critical risks, such as blood flow issues and respiratory complications, which the surgical team addressed in their final approach.
- Outcome : The surgery was a monumental success and concluded 8 hours sooner than expected, reducing the twins’ time under anesthesia and improving the likelihood of recovery.
Global Implementation
Surgical models are now being widely adopted by hospitals worldwide. Institutions such as Stanford Medicine and Mayo Clinic are using 3D printed models to approach unique cases, including rare cancers and facial reconstructions, proving this technology’s adaptability to a variety of medical disciplines.
6. 3D Printing in Drug Delivery Devices
Another groundbreaking application of 3D printing in healthcare is its ability to personalize drug delivery devices. Through additive manufacturing, drug systems are now being optimized for targeted delivery, increased bioavailability, and customized dosage forms . This creates better healthcare outcomes, especially for patients with chronic diseases or complex conditions requiring localized treatment.
How 3D Printing Works in Drug Delivery
Unlike traditional pill manufacturing, 3D printing enables the production of pills and implants in unique configurations or sizes tailored to the individual patient’s biological needs. For example, time-released polymer capsules release drugs gradually over a specific timeframe, reducing dosing frequency and ensuring treatment consistency.
Case Study: The FDA-Approved Spritam Epilepsy Drug
In 2015, the American pharmaceutical company Aprecia made history by launching Spritam , the first FDA-approved 3D-printed epilepsy drug.
- Technology Used : Aprecia used ZipDose technology , which allowed them to create highly porous pills that dissolve almost instantly when placed on the tongue. This was particularly beneficial for epilepsy patients who might have difficulties swallowing traditional tablets.
- Results : The rapid-dissolve technology improved the drug’s absorption rate and ensured that patients received the exact dose of medication every time.
- Wider Implications : This success opened doors for pharmaceutical companies to explore broader applications of 3D-printed medications, including personalized cancer treatments and antibiotics.
7. Assistive Devices: Enhancing Patient Mobility and Independence
Assistive devices, such as wheelchairs, orthoses (braces), exoskeletons, and hearing aids, are crucial for improving the quality of life for individuals with disabilities or mobility challenges. However, traditional assistive technology often lacks the customization needed to match unique patient needs. This limitation has made many devices uncomfortable or inefficient, resulting in suboptimal patient outcomes. Enter 3D printing , which has emerged as a game-changer by producing highly tailored and affordable assistive devices designed exclusively for individual users.
How 3D Printing Benefits Assistive Devices
3D printing’s precision allows manufacturers to create devices that are not only personalized but also lightweight and durable. Orthoses, for example, can now be designed to fit a child’s growing limbs perfectly, and exoskeletons can align exactly with a patient’s spinal structure. The process is faster and more cost-effective compared to conventional manufacturing, enabling quicker access for patients who need immediate assistance.
In addition, 3D scanning technology ensures that the devices fit comfortably, reducing pressure sores and other injuries commonly associated with poorly-fitted equipment. This broader level of accessibility has empowered healthcare practitioners to offer assistive technologies to underserved regions, where such devices were previously unavailable due to cost constraints.
Case Study: Customized Hearing Aids for Better Sound Quality
Hearing aids represent one of the largest categories of assistive devices benefiting from 3D printing. Companies such as Sonova and Widex have reshaped the industry by leveraging 3D printing for individualized ear canal models.
- Customization Process : Patients’ ear canal shapes are scanned using digital tools, and this data is used to design a hearing aid shell that fits perfectly inside the ear. The shells are then printed using specialized resin materials.
- Improved Comfort and Performance : The better fit ensures that the hearing aid delivers sound directly to the eardrum without slipping, thereby improving sound quality while eliminating discomfort.
- Mass Adoption : Today, as many as 97% of custom hearing aids are manufactured using 3D printing technologies, enabling quicker production. Patients can receive a hearing aid within a week, compared to the traditional 2–3 weeks.
Affordable Braces and Orthoses
Apart from hearing aids, 3D printing is revolutionizing orthoses for conditions like scoliosis or fractures that require braces. Traditionally, creating braces involves a time-consuming manual process, which can also be highly uncomfortable for patients during the casting phase. 3D printers, conversely, use digitized imaging to create braces that fit snugly around the torso, spine, or limb, with drastic reductions in time and cost.
Case Study: 3D-Printed Exoskeleton for Paraplegic Patients
Ekso Bionics , a leader in wearable robotics, has partnered with 3D printing experts to develop assistive exoskeletons tailored to paraplegic patients.
- Individualized Fit : The exoskeleton frame is 3D printed to conform perfectly to each patient’s body, ensuring alignment with joints and improved weight distribution.
- Life Improvements : With such devices, patients experience restored mobility, enabling them to walk with assistance. For some, this has also significantly contributed to improved mental well-being by giving them independence previously unattainable with traditional mobility aids.
Global Reach in Resource-Limited Settings
3D-printed assistive devices are increasingly being deployed in resource-poor settings. Organizations like FabLab Namibia train local communities to create orthoses and prosthetic extensions using affordable 3D printers, ensuring that patients across developing nations can gain access to such technologies.
8. Medical Education and Surgical Training with 3D Printed Models
The world of medical education has traditionally relied on cadavers or synthetic models for training purposes, but these have limitations in availability, cost, and fidelity to real human anatomy. 3D printing has introduced a revolution in medical education by providing lifelike anatomical replicas that are more accessible, customizable, and cost-effective. These models allow students and healthcare professionals to practice surgical techniques, hone their skills, and prepare for real-world operations without risking harm to patients.
Advantages of 3D Printed Models in Education
- Realistic Anatomy : Additive manufacturing can produce highly detailed replicas of tissues and organs, mimicking the texture, density, and intricacy of human anatomy.
- Custom Models : Models can be tailored to reflect the unique features of a particular patient, enabling student practitioners to experience challenges that cannot be addressed with generalized models.
- Cost-Effectiveness : Printing anatomical models costs a fraction of maintaining cadavers, making it possible for schools and hospitals with limited budgets to access reliable training tools.
Case Study: Harvard Medical School’s Innovation in Training
Medical students at Harvard Medical School have embraced the use of 3D-printed organ models during their surgical residency programs.
- The Project : Harvard’s bioengineering department developed a 3D replica of the human kidney to help students practice conducting transplants. The model not only included the kidney’s complex vascular system but also mimicked the resistance of human tissue when cut.
- Results : Students who trained with the model reported a 40% increase in skill confidence , particularly in handling tricky procedures involving suturing organs and treating vascular leaks.
- Scaling the Initiative : Encouraged by its success, Harvard now uses similar models to simulate liver, brain, and heart surgeries.
Surgeons Relying on Models for Real-World Cases
Among practicing surgeons, 3D-printed models are highly valued for pre-surgical planning. Patients with complex conditions, such as arterial abnormalities or rare genetic defects, often require personalized surgical approaches. Medical teams now use patient-specific 3D models generated from CT or MRI scans to perform mock surgeries prior to the actual operation. This preparation statistically reduces errors and saves time in the operating theater.
Expanding Accessibility Globally
Nonprofit organizations are using 3D printing to build models for educational purposes in countries where medical resources are scarce. For example, 3D4MD , a social enterprise, trains local physicians in rural areas to print anatomical replicas, improving the skillsets of community healthcare workers.
9. Low-Cost Medical Devices for Developing Regions
In many low-income and remote regions, access to basic medical tools and devices remains a significant challenge due to high costs and logistical barriers. 3D printing has emerged as a remarkable enabler of affordable solutions, reducing dependency on traditional supply chains and empowering local communities to produce essential medical tools on demand.
Applications in Resource-Limited Settings
From basic surgical equipment, such as clamps and forceps, to diagnostic tools like otoscopes, 3D printing enables the production of life-saving instruments with locally available materials. This addresses the pervasive issue of equipment shortages in smaller clinics and field hospitals.
Case Study: Umbilical Cord Clamps in Kenya
In rural Kenya, the Africa Biomedical Engineering Consortium (ABEC) used 3D printing to produce umbilical cord clamps for maternity wards.
- Problem : Many clinics lacked hygienic clamps, increasing the risk of infection during childbirth.
- Solution : ABEC designed lightweight, disposable 3D-printed clamps that could be produced for less than $0.10 per unit , ensuring affordability for budget-strapped clinics.
- Impact : Within a year, hundreds of hospitals had adopted these clamps, reducing neonatal infections by over 40% in supported regions.
10. Revolutionizing the Aerospace Industry with Medical 3D Printing
While aerospace applications of 3D printing are already widely recognized, its intersection with healthcare is opening new frontiers. The aerospace industry has leveraged 3D printing to develop durable, lightweight, and high-performance materials for spacecraft and aviation needs. Interestingly, these technologies are now being adapted to healthcare applications, where similar features — endurance, precision, and weight reduction — become crucial factors in designing ergonomic medical tools and devices.
Adaptation for Portable Medical Devices
Take, for example, portable healthcare devices such as field-ready diagnostic kits or compact ventilators used in disaster zones. 3D-printed designs originally created for aerospace use are easily repurposed to create medical devices that are effective, durable, and easy to deploy in remote, high-stress environments.
Case Study: NASA-Inspired 3D Printed Ventilators
When the COVID-19 pandemic created a global ventilator shortage, aerospace engineers played a surprising role in meeting healthcare demands. In 2020, engineers working on NASA Jet Propulsion Laboratory projects redirected their 3D printing expertise to create a lightweight, portable ventilator called VITAL (Ventilator Intervention Technology Accessible Locally) .
- Quick Production Turnaround : The prototype was designed and 3D-printed within 37 days, demonstrating the unparalleled speed at which additive manufacturing can respond to crises.
- Robust Engineering : Leveraging energy-efficient materials regularly used in space exploration, the ventilator could operate continuously in harsh, resource-limited settings without requiring high maintenance.
- Access for Healthcare Systems : With open-source licensing, manufacturers globally were able to produce ventilators where they were needed most, saving countless lives.
Future Potential in Aerospace-Medical Synergy
NASA and other aerospace giants continue to explore how 3D printing can catalyze biomedical experiments aboard spacecraft. These include bioprinting human tissue under low-gravity conditions to study organ development or manufacturing medical tools in real-time for long-duration space missions. As this partnership grows, the trickle-down effects on Earth-based healthcare may revolutionize how rapid innovation takes place in areas like emergency medicine and disaster relief.
3D Printing, A Game-Changer in Healthcare
As we’ve explored, 3D printing is far more than just an emerging technology — it has become a cornerstone for innovation in modern medicine. Prosthetics that empower limb-difference patients, bioprinted tissues aiming to address organ shortages, precise surgical preparations, and low-cost medical tools have all proven the unparalleled versatility of additive manufacturing.
This transformative technology has also expanded accessibility, making healthcare more inclusive for underserved communities and economically disadvantaged regions. By reducing costs, improving customization, and addressing logistical challenges, 3D printing is helping to bridge the global healthcare gap one innovation at a time
As research continues to drive adoption and scalability, we’re likely to see entirely new possibilities arise, from on-demand medical manufacturing in hospitals to longer-term projects such as bioprinted organs. The future of healthcare, intricately tied to 3D printing, is undoubtedly bright, and society is just beginning to scratch the surface of its potential.
FAQs
1. What is 3D printing, and how is it used in healthcare?
3D printing, also known as additive manufacturing , is a process where three-dimensional objects are built layer by layer using specialized machines and materials such as plastics, metals, ceramics, or biological substances (e.g., bioinks).
In healthcare, 3D printing is used to create customizable and tailored solutions for patients. Applications include:
- Manufacturing prosthetics and orthoses designed to fit unique patient anatomies.
- Printing surgical planning models , allowing surgeons to rehearse operations before the actual procedure.
- Producing implants and medical devices like dental crowns, hearing aids, and joint replacements.
- Bioprinting tissues and exploring living organ printing to address the chronic shortage of organ donors.
This makes 3D printing an invaluable tool for high precision and patient-specific care.
2. What are the main benefits of 3D printing in healthcare?
The primary benefits of 3D printing in healthcare include:
- Personalization : Devices such as prosthetics, implants, and orthoses can be tailored to match an individual’s exact anatomy.
- Faster Turnaround : Complex medical devices, surgical tools, or even models can be produced in days rather than weeks or months.
- Cost-Effectiveness : Traditional manufacturing methods are expensive due to the use of molds and labor. 3D printing eliminates many of these costs, making healthcare innovations more accessible.
- Global Accessibility : Clinics and hospitals in underserved regions can use 3D printers to produce necessary tools locally, reducing reliance on expensive imports.
- Surgical Precision : Surgeons use models of organs and bones to better prepare for complex procedures, reducing risks and improving outcomes.
3. How does 3D printing create affordable prosthetics?
3D printing makes prosthetics affordable by eliminating expensive manufacturing processes and reducing material waste.
- Traditional prosthetics often require specialized molds, making them expensive. Costs can start at $5,000 and exceed $50,000 depending on customization and materials.
- 3D-printed prosthetics , on the other hand, are designed digitally using imaging data (like CT or MRI scans). These designs are printed layer by layer, significantly lowering production costs, sometimes to as low as $50–$100 per prosthetic .
Additionally, the digital nature of 3D-printed prosthetics allows for ongoing adjustments as patients grow or their needs change, particularly for children who require regular replacements. Global networks like e-NABLE empower local communities to produce affordable, custom-fit prosthetics using basic 3D printers.
4. What materials are used in 3D printing for healthcare?
The materials used in 3D printing for healthcare vary based on the application. Here are the most common materials:
- Plastics and Polymers : Used for prosthetics, orthoses, and surgical models. Popular materials include PLA (Polylactic Acid) and ABS (Acrylonitrile Butadiene Styrene) because they are lightweight, durable, and biocompatible.
- Metals : Titanium and titanium alloys are used to make durable joint implants and orthodontic components due to their strength and biocompatibility.
- Ceramics : Used for dental implants and bone grafts, ceramics are favored for their stability and compatibility with human bones.
- Bioinks : Specialized bioinks made from living cells and biocompatible scaffolds are used in bioprinting tissues and organ prototypes .
- Hydrogels : Ideal for printing soft tissues like cartilage and skin.
The choice of material depends on the function, durability requirements, and patient-specific factors.
5. Is bioprinting organs a current reality, and what does the future hold?
Bioprinting fully functional and transplantable organs is not yet a reality , but significant progress has been made in the field. Researchers are currently developing bioprinted tissues and organ prototypes to address specific challenges.
Progress So Far
- Printed Tissues : Lab-grown tissues for drug testing and research are now a standard part of medical innovation. Bioprinted skin grafts for burn victims have shown great promise.
- Proof of Concept for Organs : Researchers at Tel Aviv University recently printed a miniature, functional heart that mimics human cardiac structures, although it lacks sufficient size and complexity for transplantation.
Future Outlook
In the coming decades, bioprinting could solve organ donor shortages globally. The technology has the potential to print functional hearts, livers, and kidneys using a patient’s own cells, eliminating risks of organ rejection and drastically reducing wait times.
6. How do 3D-printed surgical models improve surgeries?
3D-printed surgical models provide surgeons with exact, life-sized replicas of organs, bones, or other anatomical structures based on a patient’s MRI or CT scans. These models allow surgeons to practice and rehearse operations before entering the operating room.
Benefits of Surgical Models:
- Improved Precision : Surgeons can identify potential challenges earlier, ensuring less risky and more accurate interventions.
- Reduced Operating Time : Knowing the detailed anatomy beforehand shortens surgery durations, reducing risks associated with prolonged anesthesia.
- Enhanced Training : Models allow medical students and surgical teams to practice on realistic replicas.
For example, Boston Children’s Hospital used 3D heart models for pediatric surgeries in children with rare heart defects, reducing risks and improving surgical outcomes.
7. How was 3D printing used during the COVID-19 pandemic?
During the COVID-19 pandemic, 3D printing played a crucial role in addressing supply shortages for medical equipment, such as personal protective equipment (PPE), ventilator parts, and diagnostic tools.
Examples of 3D-Printing Success During the Pandemic:
- Ventilators : NASA’s “VITAL” ventilator, created during COVID-19, relied on 3D printing tech to produce low-cost, emergency-ready ventilators that were used in hospitals worldwide.
- Face Shields and Masks : Makers and organizations worldwide used 3D printers to produce millions of face shields and N95-style masks for frontline workers.
- Swabs for Testing : 3D printers ensured the large-scale production of nasopharyngeal swabs when traditional manufacturing was overwhelmed.
This rapid response showcased the versatility and scalability of 3D printing in addressing global crises.
8. How does 3D printing benefit developing nations?
In developing countries, where access to medical tools is limited, 3D printing is providing locally-produced equipment at drastically reduced costs. By bypassing traditional manufacturing and shipping bottlenecks, clinics and hospitals are able to create essential devices such as:
- Prosthetics for individuals with limb loss, often at one-tenth the cost of traditional options.
- Umbilical cord clamps and surgical tools (e.g., forceps and retractors).
- Diagnostic Devices like stethoscopes made on-demand at field hospitals.
Organizations like Field Ready and 3D4MD train communities in developing nations to take advantage of 3D printing technology. Local production empowers healthcare workers to innovate even in low-resource settings.
9. How reliable are 3D-printed implants and medical devices?
3D-printed implants, such as cranial plates and joint replacements, are highly reliable and have received regulatory approvals worldwide. Several medical implants created using 3D printers, such as orthopedic joints, spinal cages, and dental crowns, are already being used in surgeries.
Advantages of 3D-Printed Implants:
- Exact Fit : Implants are customized to match the patient’s anatomy, reducing the chances of post-surgical complications.
- FDA Approval : Many 3D-printed implants comply with strict safety standards and biocompatibility benchmarks. For instance, 3D titanium implants used in cranial surgeries ensure robust performance and durability.
10. What is the future of 3D printing in healthcare?
The future of 3D printing in healthcare holds limitless potential. As the technology advances, the following developments are likely to dominate:
- Bioprinted Organs : The eventual creation of functional, transplantable organs.
- Hospital-Based Printing : Hospitals may adopt on-site 3D printers for real-time production of surgical tools, implants, and personalized devices.
- Increased Global Access : Wider adoption in low-income regions, improving affordability and accessibility significantly.
Overall, 3D printing is paving the way for more efficient, inclusive, and personalized healthcare systems .