How the Automotive Industry Uses 3D Printing to Innovate
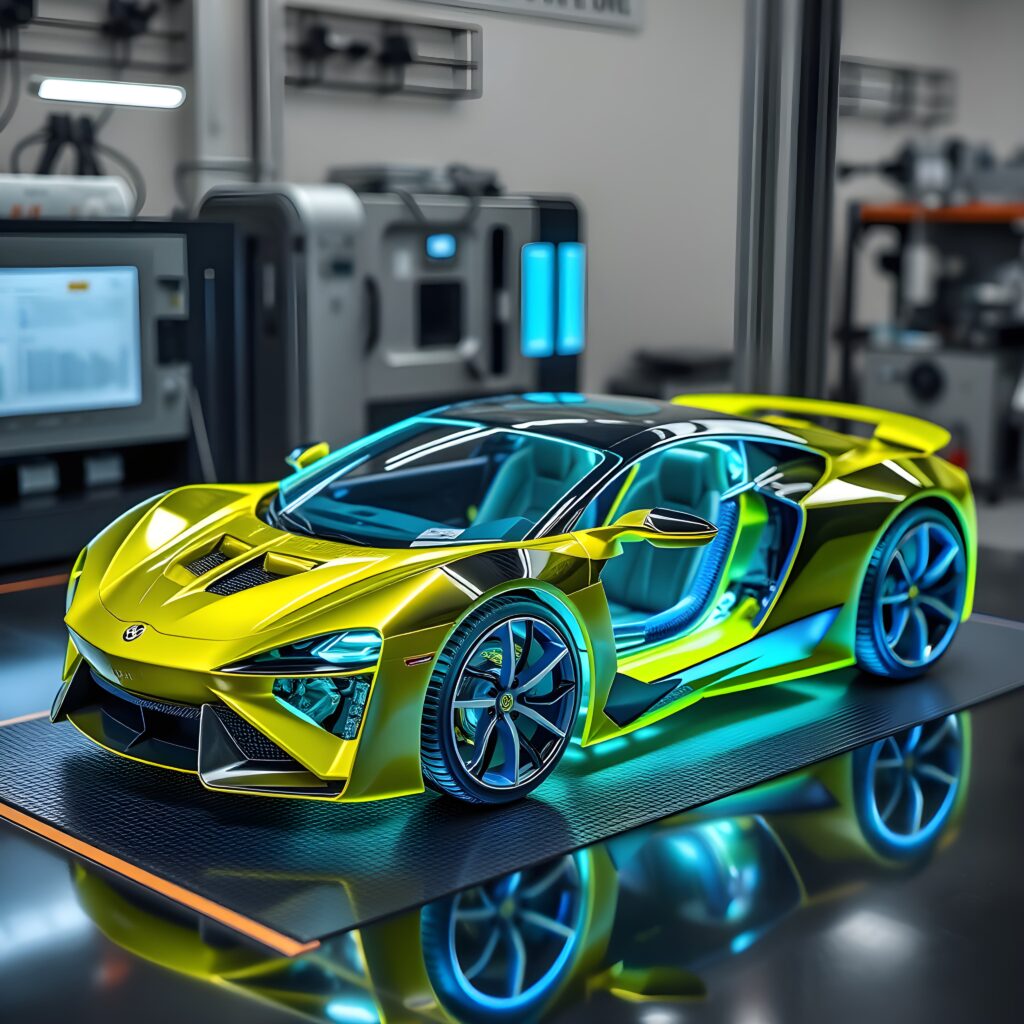
See how the automotive industry leverages 3D printing from prototyping to end-use parts. Explore innovations from Porsche, Ford, and Tesla.
Driving Automotive Innovation with 3D Printing
The automotive industry has always been at the forefront of technological advancement, incorporating cutting-edge innovations to optimize productivity, design, and performance. Among these technologies, 3D printing (also known as additive manufacturing) has emerged as a transformative force in recent years. By enabling manufacturers to create parts with unprecedented precision, reduced weight, and optimized geometry, 3D printing has revolutionized how cars are designed, prototyped, and produced.
From rapid prototyping in research and development (R&D) to creating lightweight end-use components , 3D printing is breaking barriers that once limited traditional manufacturing. In fact, reports suggest that the global automotive 3D printing market is projected to exceed $12 billion by 2030 due to the wide-scale adoption of this technology for both prototyping and large-scale production needs.
Leading players like Tesla , Porsche , Ford , and BMW are leveraging 3D printing to improve vehicle performance, reduce production costs, and drive innovation in electric and autonomous vehicles. In this article, we’ll explore the real-world applications of 3D printing in the automotive industry through detailed case studies , expert insights, and a closer look at what makes this technology a game-changer.
Rapid Prototyping: Speeding Up Innovation
3D printing is most commonly associated with rapid prototyping , a process that allows automotive design teams to quickly create and test new components. Traditional prototyping methods often require weeks or even months to develop and refine a single prototype, making them time-consuming and expensive. In contrast, 3D printing can produce parts in hours or days, offering significant time and cost savings.
Benefits of Rapid Prototyping with 3D Printing
- Cost Savings : Unlike traditional manufacturing, 3D printing eliminates the need for expensive molds or machining processes.
- Faster Design Iterations : Engineers can print several design iterations, test them in real-life scenarios, and refine the models without significant delays.
- Complex Designs Made Simple : Components with intricate geometries that are difficult or impossible to produce with traditional tools can be created with ease.
Case Study: Ford’s Prototyping Revolution
Ford Motor Company has fully embraced 3D printing to accelerate its vehicle development lifecycle . At Ford’s Advanced Manufacturing Center in Michigan, engineers use additive manufacturing technologies to develop and test prototypes for nearly every vehicle in their fleet.
- Time Reduction : A process that used to take Ford engineers up to 4 months now takes only a few days with 3D printing.
- Cost Efficiency : Ford has reduced prototyping costs by up to 50% per unit.
- Breakthrough Designs : One notable example is their 3D-printed brake tooling , which reduced the part’s total weight by over 30%, boosting both efficiency and durability.
Lightweight Components: Boosting Fuel Efficiency and Sustainability
Weight reduction has become a critical goal for the automotive industry, particularly as manufacturers prioritize fuel savings in traditional vehicles and range optimization in electric vehicles (EVs) . Here, 3D printing has played an instrumental role by unlocking the potential of lightweight designs and advanced materials such as carbon fiber composites and metal alloys .
Why Lightweighting Matters
- Lighter vehicles consume less fuel or extend the driving range of EVs, reducing greenhouse gas emissions.
- Lightweight components also improve vehicle acceleration, handling, and overall performance.
Case Study: Porsche’s 3D-Printed Electric Vehicle Components
Porsche is at the forefront of integrating 3D printing into its electric vehicle production, particularly to reduce the weight of engines and structural components.
- Electric Drive Housing : Porsche partnered with metal 3D printing experts to create a highly optimized electric drive housing that is significantly lighter than traditionally cast versions. The new housing is roughly 10% lighter , offering better weight distribution and range efficiency for Porsche EVs.
- Exhaust Housing Parts : The company has also used 3D printing to build more efficient exhaust housings for their performance models. This design reduces backpressure and optimizes exhaust flow, leading to improved power output and environmental benefits.
- Sustainability : Porsche’s manufacturing process now relies on recycled metal powders , reducing material waste by up to 70%.
Future Applications
By combining generative design principles (where AI optimizes the design of a part) with 3D printing, manufacturers like Porsche are producing lightweight, performance-enhancing components for everything from gearboxes to body panels.

Production-Ready Parts: Moving Beyond Prototypes
While 3D printing was initially limited to prototyping, advancements in materials and printing technology have made it possible to manufacture end-use parts that meet the high standards of durability and precision required in the automotive industry.
Real-Time Manufacturing
Automakers now use 3D printing for on-demand production, eliminating the need for large inventories of spare parts. By incorporating 3D printers into their supply chains, manufacturers can produce components as needed, whether for production vehicles or aftermarket repairs.
Case Study: BMW’s 3D-Printed Car Interiors
BMW is a leader in using 3D printing for end-use part production , particularly in its customization and luxury divisions:
- Customized Parts for Clients : The BMW i8 Roadster introduced 3D-printed roof brackets , which were 44% lighter than those created with conventional methods.
- Mass Customization : Customers can now personalize certain interior parts, such as dashboard covers and gear levers, directly through their dealership. These items are manufactured on-demand using BMW’s in-house 3D printers.
- Scalability : BMW has invested in over 30,000 3D-printed parts annually for its production vehicles, making it one of the top adopters of additive manufacturing worldwide.
The Future of Mass Production
With innovations like multi-material printing and large-scale additive manufacturing , automakers are gradually integrating 3D printing into assembly lines, bridging the gap between prototypes and fully engineered production components.
Tooling and Fixtures: Reducing Costs on the Factory Floor
Another essential application of 3D printing within the automotive sector is the production of tools, jigs, and fixtures used on assembly lines. Rather than sourcing these parts from third-party manufacturers, companies can now print high-quality tools in-house, saving time and reducing costs.
Case Study: Volkswagen Autoeuropa Uses Additive Tooling
Volkswagen Autoeuropa, one of the largest car manufacturing facilities in Portugal, saved over $150,000 annually by producing fixtures and toolings via 3D printing.
- Faster Production : The tools that previously required 55 days to manufacture could now be printed in 10 days.
- Cost Reduction : A single fixture, costing $450 through conventional methods, was reduced to $150 using 3D printers.
- Increased Customization : By printing tools internally, Volkswagen was able to create ergonomic jigs that improved worker efficiency on the factory floor.
Customized Bodywork: Tailoring Cars to Customer Preferences
One of the most exciting applications of 3D printing in the automotive industry is its ability to facilitate personalized designs and customized bodywork . Unlike traditional manufacturing, where molds and templates restrict design variations, 3D printing enables automakers to offer bespoke vehicles tailored to individual customer preferences.
Why Customization Matters
With the rise of luxury vehicle divisions and increasing demand for unique, one-off designs, automakers are shifting toward personalization. From custom dashboards to entirely reworked car exteriors, 3D printing bridges creativity and practicality for high-end and limited-edition cars.
Case Study: MINI’s Personalization Program
MINI, part of the BMW group, has embraced 3D printing for its MINI Yours Customized Program , allowing customers to personalize various car components.
- Custom Dashboard Inlays : Customers can design their own dashboard panels using online tools, creating unique patterns, colors, or even engraved messages. These designs are then 3D printed and shipped directly to the customer or dealership for installation.
- Personalized Side Scuttles : Owners can customize side scuttles (the trim pieces around the car’s side indicators), adding names, logos, or patterns.
- Streamlined Process : By using 3D printing, MINI eliminates the need for mass production, reducing material waste while delivering tailor-made parts.
Luxury and Exotic Customizations
For high-performance and luxury brands like Bugatti and Aston Martin, where exclusivity is paramount, 3D printing has unlocked unprecedented innovations. Bugatti, for example, has used titanium 3D printing to create custom brake calipers featuring intricate, lightweight designs that are entirely unique to each model.
Future Trends
Additive manufacturing is expected to play a significant role in further expanding customization for electric and autonomous cars. Interior components, exterior trims, and lightweight performance parts could all be tailored to meet precise customer needs in the coming years.
Sustainability: Eco-Friendly Manufacturing with 3D Printing
As climate change continues to shape consumer expectations and government regulations, the automotive industry is under immense pressure to adopt sustainable practices . 3D printing offers a pathway to eco-friendly manufacturing by significantly reducing material waste, energy usage, and carbon emissions.
How 3D Printing Enhances Sustainability
- Reduced Material Waste : Additive manufacturing uses only the exact material needed to construct a part, unlike traditional subtractive processes (e.g., milling), which produce significant scrap material.
- Energy Efficiency : Lightweight vehicle components created through 3D printing lead to higher fuel efficiency, directly lowering emissions. For EVs, lighter materials increase battery efficiency and extend driving ranges.
- Recyclable Materials : Many automakers, such as Porsche and BMW, now use recycled metals and polymers in 3D printing to further reduce their environmental impact.
Case Study: Toyota’s Sustainable 3D Printing Practices
Toyota has incorporated 3D printing into its sustainability initiatives by using recycled plastics to manufacture lightweight decorative parts for EV interiors.
- Circular Economy Focus : Toyota collects discarded plastics from production scraps and old vehicles, converting them into printable materials.
- Enhanced Recycling : Their closed-loop recycling model allows them to reuse the same material multiple times across different parts.
- Results : This approach has reduced interior part production waste by over 40% in Toyota’s latest vehicle lines, including the Prius Prime.
Future Potential
Automakers, including Tesla, are exploring carbon fiber-based polymers for 3D printing, enabling even lighter and stronger components with minimal environmental impact.
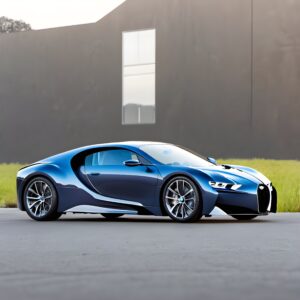
Spare Parts On-Demand: Addressing Supply Chain Challenges
One of the most disruptive uses of 3D printing in the automotive sector is in the production of spare parts on-demand . Traditionally, automakers have relied on extensive warehouses and global logistics networks to store and distribute spare parts. However, 3D printing is challenging this model by enabling decentralized, real-time manufacturing of components.
Benefits of On-Demand Spare Parts
- Reduced Inventory Costs : By eliminating the need to store massive inventories, companies save millions annually.
- Faster Repairs : 3D printed parts can be produced and delivered to customers or repair shops in a fraction of the time compared to standard shipping.
- Legacy Parts : 3D printing makes it feasible to recreate discontinued or rare car parts for vintage models, enhancing the lifespan of older vehicles.
Case Study: Volkswagen’s 3D Spare Parts Program
Volkswagen leverages 3D printing to produce replacement parts for its older models that are no longer in production.
- Legacy Components : Parts such as gear knobs for the Golf GTI from the 1980s are now printed on-demand to cater to vintage collectors.
- Reduction in Lead Times : One such part that previously required six weeks to produce now takes just a few days with 3D printing.
- Global Reach : By using a network of printing hubs, Volkswagen ensures spare parts can be manufactured closer to the customer, reducing carbon emissions related to transportation.
Enhancing Electric Vehicles (EVs) and Autonomous Vehicles (AVs)
3D printing has become a key enabler in the development of electric vehicles (EVs) and autonomous vehicles (AVs) . From lightweight materials to battery components and aerodynamic designs, additive manufacturing is tailoring new solutions for next-generation vehicles.
Lightweighting EVs for Greater Range
One of the greatest challenges with EVs is maximizing battery efficiency. By reducing weight without sacrificing structural integrity, 3D printing helps extend EV range , reducing the frequency of recharging.
Case Study: General Motors’ 3D-Printed EV Components
General Motors (GM) partnered with additive manufacturing firms to produce lightweight brackets and structural components for the Chevrolet Bolt EV.
- Material Innovation : GM used high-strength aluminum alloys to reduce the vehicle’s weight by 15%.
- Improved Efficiency : The new components increased battery efficiency, extending the Bolt’s range by an additional 7%.
Custom Sensors for AVs
3D printing also enables AV manufacturers to create custom sensors and housings that are tailored to vehicle designs. These sensors monitor surroundings in real-time, ensuring accuracy and safety.
Cost-Benefit Analysis: Why Automakers Invest in Additive Manufacturing
The initial costs of adopting 3D printing (e.g., purchasing printers, sourcing materials) can be high, but the long-term savings and benefits far outweigh the costs.
Key Advantages Automotive Giants Cite
- Faster Time-to-Market : Streamlining production processes allows automakers to beat competitors to market.
- Reduced Waste : Additive manufacturing minimizes material waste by up to 70%.
- Customization Capabilities : Bespoke designs catered to consumer demands result in higher sales in luxury sectors.
- Sustainability : Reduced emissions and energy savings enhance companies’ compliance with environmental regulations.
Expert Opinions and Future Trends in Automotive 3D Printing
Expert Insights
- Josef Kunkela, Porsche R&D Lead, remarks: “3D printing is no longer a prototyping-only tool; it’s shaping the future of production parts for electric and lightweight vehicles.”
- BMW’s Additive Center predicts that true mass production with fully automated 3D printing systems will be achieved within the next decade.
Trends to Watch
- Multi-Material Printing : Automakers are experimenting with parts combining metals and plastics.
- Real-Time Printing in Factories : Fully integrated additive manufacturing systems may completely replace traditional supply chains.
- Carbon-Neutral 3D Manufacturing : More automakers will adopt 3D printing technologies powered by renewable energy.
FAQs
1. How is 3D printing used in the automotive industry?
3D printing is primarily used in the automotive industry for prototyping , manufacturing end-use parts , creating lightweight components , producing custom designs , and enabling on-demand spare part production . For a deeper dive, visit 3D Printing Industry and explore their automotive section.
2. What materials are used for 3D printing in automotive applications?
Commonly used materials for automotive 3D printing include:
- Thermoplastics (e.g., ABS and nylon) for lightweight and durable components.
- Metal powders (e.g., titanium and aluminum) for structural parts and engine components.
- Carbon composites for high-strength, lightweight applications.
To understand material options further, check out this resource from 3D Hubs .
3. Are 3D-printed car parts reliable and safe?
Yes, 3D-printed components meet automotive industry standards for durability and safety. Materials like titanium alloys and carbon fiber composites ensure exceptional strength and reliability. BMW is actively using 3D-printed parts in production vehicles like the BMW i8 and Mini, demonstrating their feasibility.
4. What are the benefits of 3D-printed spare parts for the automotive industry?
The key benefits include reduced inventory costs, faster production, and the ability to recreate legacy parts for older cars. Companies like Volkswagen are using additive manufacturing to produce replacement parts on demand, ensuring availability even for discontinued vehicle models.
5. How does 3D printing contribute to sustainability in the automotive industry?
3D printing contributes to eco-friendly manufacturing by minimizing material waste, using recycled materials, and reducing energy consumption. According to Porsche Newsroom , the company now integrates recycled metal powders into its 3D printing processes to lower its carbon footprint.
6. What role does 3D printing play in electric and autonomous vehicles (EVs and AVs)?
3D printing enables lightweight designs, which are essential for improving EV battery efficiency and extending driving range. For AVs, it helps build customized components like sensor housings and aerodynamic trims. Learn more about how General Motors is implementing this technology in autonomous vehicle research.
7. How is 3D-printed customization impacting the luxury and sports car market?
Luxury brands like Bugatti and MINI use 3D printing to offer tailor-made designs, enhancing customer satisfaction. Bugatti, for example, uses 3D-printed titanium brake calipers , which are among the world’s largest functional titanium parts. For more examples, visit Bugatti’s Innovations page.
8. What challenges do automakers face with implementing 3D printing on a large scale?
Challenges include high initial setup costs, longer production times for mass manufacturing, and limited material choices for high-volume applications. For further insights, check this analysis of automotive 3D printing challenges .
9. Which automakers are leading in 3D printing adoption?
Leading companies leveraging 3D printing include:
- Porsche : Lightweight EV components and high-performance metal parts.
- BMW : Customized interior/exterior designs and production parts.
- Ford : Streamlined prototyping processes.
To explore examples in detail, check Porsche Engineering News .
10. What’s the future of 3D printing in the automotive industry?
The future includes fully integrated additive manufacturing systems for mass production, lighter electric vehicle components, and the potential for decentralized manufacturing hubs . According to Market Research , the automotive 3D printing market is projected to grow to $12 billion by 2030.
If you found this helpful, stay tuned to our blogs!!