3D Printing in Aerospace: Reducing Costs and Improving Performance
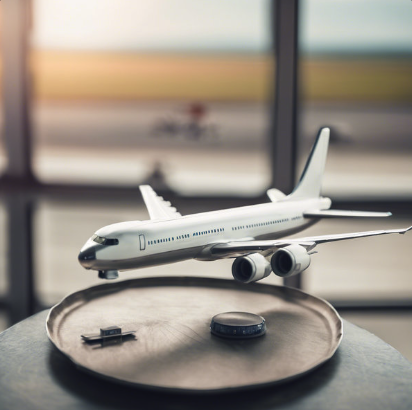
The aerospace industry has always been at the forefront of adopting innovative technologies, and 3D printing is no exception. This transformative technology, also known as additive manufacturing, is redefining how components are designed, manufactured, and maintained. By leveraging 3D printing, the aerospace sector is achieving significant cost reductions, improving performance, and fostering sustainability. This article delves into the various ways 3D printing is revolutionizing the aerospace industry, highlighting recent advancements and real-world applications.
The Role of 3D Printing in Aerospace
Cost Reduction
One of the primary drivers of 3D printing adoption in aerospace is its potential to reduce costs. Traditional manufacturing methods often involve subtractive processes that result in significant material wastage. In contrast, additive manufacturing uses only the material needed to create the component, drastically reducing waste. For example:
-
Material Savings: High-performance materials like titanium are expensive, and minimizing waste directly reduces costs.
-
Tooling Elimination: 3D printing allows for direct manufacturing of parts without the need for costly tooling, further cutting expenses.
-
Supply Chain Simplification: Components can be produced on-demand and closer to the point of use, reducing inventory and logistics costs.
Performance Improvement
3D printing enables the creation of complex geometries that are impossible or highly challenging to achieve with traditional methods. These designs enhance performance by optimizing weight, strength, and aerodynamics. For instance:
-
Lightweight Structures: Aerospace companies use 3D printing to create lighter components, which improves fuel efficiency and payload capacity.
-
Enhanced Cooling Systems: Advanced designs, such as internal cooling channels for turbine blades, improve thermal efficiency.
-
Customized Solutions: Tailored components can be created to meet specific performance requirements, enhancing overall system effectiveness.
Applications of 3D Printing in Aerospace
Engine Components
3D printing has proven to be a game-changer for engine manufacturing. Companies like GE Aviation are using additive manufacturing to produce fuel nozzles for jet engines. These nozzles are:
-
Lighter and More Durable: Reduced weight leads to better fuel efficiency, while increased durability extends component lifespan.
-
Single-Piece Construction: Traditional nozzles consist of multiple parts joined together. 3D printing allows for a single-piece design, reducing assembly time and potential failure points.
Structural Components
Aerospace structures, such as brackets and panels, are being reimagined through 3D printing. These components benefit from:
-
Optimized Topology: Designs that maximize strength while minimizing weight.
-
Material Efficiency: Reduced material usage without compromising structural integrity.
-
Rapid Prototyping: Faster production cycles enable quicker testing and iteration of designs.
Satellite Manufacturing
The satellite industry is leveraging 3D printing to streamline production and reduce launch costs. Additive manufacturing facilitates:
-
Custom Design: Satellites can be tailored for specific missions.
-
Integrated Components: Complex assemblies are consolidated into fewer parts, reducing manufacturing time and improving reliability.
-
Rapid Deployment: Faster manufacturing enables quicker response times for urgent missions.
Space Exploration
3D printing is playing a pivotal role in space exploration. NASA and other space agencies are exploring additive manufacturing for in-situ resource utilization (ISRU). For example:
-
On-Demand Manufacturing: Tools and components can be printed aboard spacecraft, reducing the need for carrying spares.
-
Habitat Construction: 3D printing technology is being developed to build structures on the Moon and Mars using local materials.
Maintenance and Repairs
3D printing is revolutionizing how maintenance and repairs are conducted in aerospace. Airlines and space agencies benefit from:
-
Reduced Downtime: Damaged parts can be printed on-site, minimizing delays.
-
Customized Repairs: Tailored solutions address specific repair needs without requiring extensive inventories.
-
Improved Sustainability: By extending the life of components, waste and costs are reduced.
Recent Advancements in Aerospace 3D Printing
Metal 3D Printing
The development of metal 3D printing technologies, such as selective laser melting (SLM) and electron beam melting (EBM), has significantly advanced the aerospace industry. These methods offer:
-
High Precision: Achieving tolerances required for critical aerospace components.
-
Material Versatility: Compatibility with a wide range of metals, including titanium, aluminum, and superalloys.
-
Improved Mechanical Properties: Components with enhanced strength and fatigue resistance.
Hybrid Manufacturing
Combining 3D printing with traditional manufacturing techniques is yielding hybrid approaches that capitalize on the strengths of both methods. This includes:
-
Cost-Effective Production: Utilizing 3D printing for complex sections and traditional methods for simpler parts.
-
Enhanced Quality: Improved surface finishes and structural integrity.
AI and Simulation
Artificial intelligence (AI) and simulation tools are being integrated into 3D printing workflows to optimize designs and predict performance. These advancements:
-
Reduce Development Time: Virtual testing accelerates the design process.
-
Enhance Reliability: Predictive analytics ensure components meet stringent aerospace standards.
-
High-Temperature Materials
Recent advancements in materials capable of withstanding extreme temperatures are expanding 3D printing applications in aerospace. These materials enable:
-
Improved Engine Performance: Components can operate at higher temperatures, increasing efficiency.
-
Expanded Mission Profiles: Materials withstand the harsh conditions of space exploration.
Challenges and Future Prospects
Certification and Regulation
Ensuring that 3D-printed components meet aerospace safety and quality standards remains a significant hurdle. Addressing this involves:
-
Rigorous Testing: Components must undergo extensive testing to ensure reliability.
-
Standardized Guidelines: Developing industry-wide standards for additive manufacturing.
Material Limitations
Expanding the range of printable materials with properties suitable for aerospace applications is critical. Innovations in material science are addressing:
-
Durability: Creating materials that can endure prolonged stress and environmental exposure.
-
Flexibility: Developing multi-material printing capabilities for integrated designs.
Scaling Production
Scaling up 3D printing for mass production poses technical and economic challenges. Solutions include:
-
Automated Workflows: Streamlining processes to increase efficiency.
-
Investment in Infrastructure: Establishing facilities equipped for large-scale additive manufacturing.
Despite these challenges, the future of 3D printing in aerospace looks promising. Emerging technologies and ongoing research are poised to address these hurdles, paving the way for wider adoption.
Environmental Impact
3D printing contributes to sustainability in aerospace by reducing waste and optimizing resource use. The technology supports:
-
Eco-Friendly Manufacturing: Less material waste and energy use compared to traditional methods.
-
Reduced Emissions: Lightweight components improve fuel efficiency, lowering carbon emissions.
-
Recyclable Materials: Advances in recycling technologies ensure minimal environmental impact.
3D printing is revolutionizing the aerospace industry by reducing costs, improving performance, and fostering innovation. From lightweight components to on-demand manufacturing in space, the possibilities are vast. As the technology continues to advance, its impact on aerospace will only grow, driving efficiency and sustainability in the sector. By embracing 3D printing, the aerospace industry is not just keeping up with the times but shaping the future of flight and space exploration. With its ability to address complex challenges and unlock new possibilities, additive manufacturing is set to become a cornerstone of aerospace innovation for years to come.
Visit our other website: https://synergypublish.com