Exentis Sells $22.4M in Metal 3D Printers to U.S. Customers: A Game-Changer for Additive Manufacturing
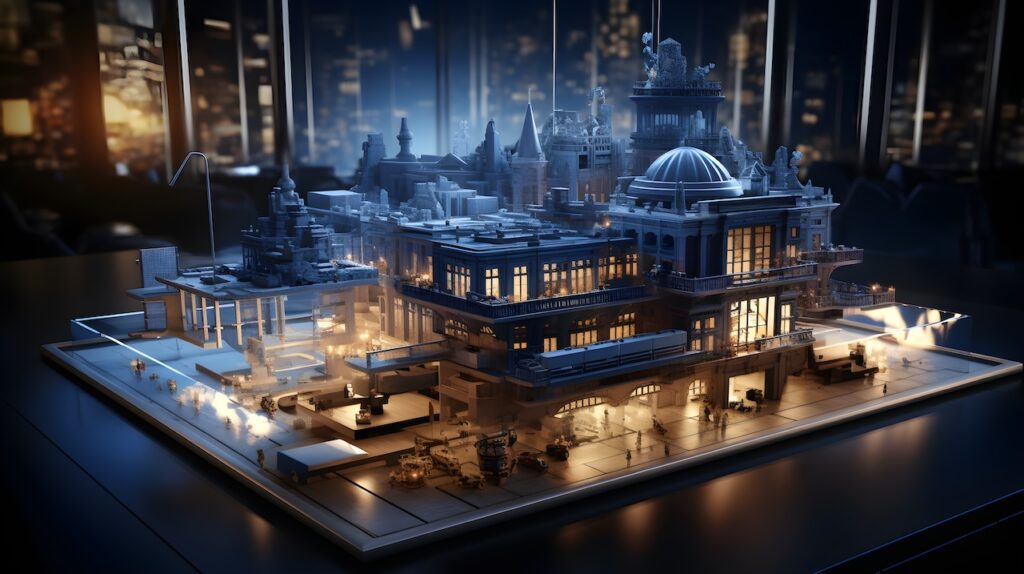
In a monumental development for the world of additive manufacturing, Exentis, a prominent player in the metal 3D printing space, has recently completed a groundbreaking deal worth $22.4 million, supplying metal 3D printers to a range of U.S.-based customers. This deal not only reflects the growing demand for metal 3D printing technology but also signals a major shift in the way industries across the United States are beginning to adopt and scale these advanced manufacturing processes.
This article explores the significance of Exentis’ $22.4 million sale, the role of metal 3D printing in modern industries, the key technologies behind Exentis’ printers, and the future of additive manufacturing in the U.S. and globally.
The Rise of Metal 3D Printing
Additive manufacturing (AM), also known as 3D printing, has come a long way since its inception in the 1980s. Originally used for prototyping and creating models, 3D printing has evolved to a point where it is now used for manufacturing complex parts and components in a wide range of industries. One of the most exciting advances in this field has been the development of metal 3D printing.
Metal 3D printing, which uses powder-based or wire-based materials to create metal parts layer by layer, has revolutionized the way companies approach production. Unlike traditional manufacturing methods, which often involve subtracting material from a solid block, metal 3D printing is an additive process that allows for greater design freedom, reduced material waste, and the creation of complex geometries that would otherwise be impossible to produce using conventional methods.
The ability to produce high-performance metal parts quickly and with precise customization has made metal 3D printing highly attractive to industries such as aerospace, automotive, healthcare, defense, and industrial machinery. The ability to fabricate components with intricate designs and reduced weight has opened up new opportunities for innovation and efficiency across the supply chain.
Exentis: A Key Player in the Metal 3D Printing Space
Exentis, based in Europe, has rapidly emerged as a leading provider of advanced metal 3D printing solutions. The company specializes in developing and manufacturing metal 3D printers that offer unique capabilities for high-precision, high-speed, and high-volume production. Exentis’ printers are known for their ability to print large parts with high material density and minimal waste, making them highly suitable for industries where cost-efficiency, precision, and performance are paramount.
The recent deal, valued at $22.4 million, sees Exentis delivering a significant number of its state-of-the-art metal 3D printers to U.S. customers across a variety of industries. These customers span sectors such as aerospace, automotive, healthcare, and manufacturing, where the ability to produce durable, high-quality metal components quickly and cost-effectively is crucial to maintaining competitive advantage.
Exentis’ rise to prominence has been fueled by its innovative approach to metal 3D printing. The company combines cutting-edge technology with a deep understanding of industry needs, making its printers some of the most advanced on the market. The $22.4 million deal demonstrates the growing confidence in Exentis’ products and signals the increasing importance of additive manufacturing in U.S. industry.
What Makes Exentis’ Metal 3D Printers Stand Out?
Exentis’ success can be attributed to several key features that set its metal 3D printers apart from competitors. These features not only make their machines attractive to U.S. customers but also reflect the future trajectory of metal 3D printing technology as a whole.
1. Large-Scale Printing Capabilities
One of the standout features of Exentis’ printers is their ability to handle large-scale printing. While many traditional metal 3D printers are limited in terms of build volume, Exentis’ machines are capable of producing parts with much larger dimensions, all while maintaining precision and quality. This feature is particularly appealing to industries such as aerospace, where large and complex components are often required.
2. High Material Density and Quality
Exentis’ printers are known for their ability to produce metal parts with high material density, which is essential for industries requiring components that can withstand high levels of stress and wear. The company uses advanced powder metallurgy techniques, which allow its machines to achieve superior material properties in the final product. This capability ensures that the metal parts produced are not only lightweight but also durable and able to withstand extreme conditions.
3. Reduced Material Waste
One of the major advantages of metal 3D printing is its efficiency in material usage. Traditional manufacturing methods often involve significant material waste, as parts are cut or machined from solid blocks. In contrast, metal 3D printing is an additive process, meaning that material is only used where it is needed, significantly reducing waste. Exentis has optimized its printers to ensure minimal material usage, leading to lower production costs and a more sustainable manufacturing process.
4. Flexibility in Materials
Exentis’ metal 3D printers support a wide range of materials, including high-performance alloys that are commonly used in demanding industries. This flexibility allows U.S. customers to choose the best material for their specific applications, whether it be stainless steel, titanium, Inconel, or aluminum alloys. The ability to use a variety of materials opens up new possibilities for innovation in industries such as aerospace, automotive, and medical device manufacturing.
5. Speed and Precision
While 3D printing is often associated with slower production speeds, Exentis has developed its technology to prioritize both speed and precision. By utilizing advanced laser systems and optimized printing algorithms, the company has managed to reduce the time required to produce high-quality metal parts without sacrificing accuracy. This capability makes Exentis’ printers particularly attractive for industries that require rapid prototyping or low-volume, high-mix manufacturing.
Impact on U.S. Industry and Manufacturing
The sale of $22.4 million worth of metal 3D printers to U.S. customers represents a significant milestone in the adoption of additive manufacturing technology in the United States. As more industries look for ways to reduce costs, improve efficiencies, and stay competitive in an increasingly globalized market, metal 3D printing is becoming an increasingly attractive option.
1. Aerospace Industry
The aerospace sector has been one of the earliest adopters of metal 3D printing, and Exentis’ printers are poised to make an impact in this area. Aerospace companies require lightweight, durable, and high-performance components for everything from engine parts to structural components. The ability to rapidly prototype and produce complex geometries with reduced weight is a game-changer in this industry. Exentis’ machines are already being used to produce parts for commercial aircraft, satellites, and defense applications, with the potential for even broader adoption in the coming years.
2. Automotive Industry
In the automotive sector, metal 3D printing is enabling manufacturers to produce lightweight components that help improve fuel efficiency and reduce emissions. Exentis’ ability to print with a variety of alloys and create custom parts in low volumes is particularly valuable for automotive OEMs (original equipment manufacturers) and suppliers who are looking to stay agile and reduce lead times. This flexibility also allows for faster design iterations and the production of bespoke components for high-performance vehicles or electric vehicles.
3. Healthcare and Medical Devices
The medical industry is another area where metal 3D printing is seeing rapid growth. Custom implants, prosthetics, and surgical tools are all areas where 3D printing has made a significant impact. Exentis’ printers are capable of producing highly accurate and biocompatible metal parts that can be tailored to individual patients. This capability is particularly important in the production of personalized medical devices that require a high degree of precision and customization.
4. Industrial Manufacturing
Beyond aerospace, automotive, and healthcare, metal 3D printing is gaining traction in general industrial manufacturing. Companies involved in the production of machinery, tools, and heavy equipment are increasingly turning to additive manufacturing to reduce production costs and improve lead times. Exentis’ printers are well-suited for this type of high-volume, precision manufacturing, making them an appealing choice for a wide variety of industrial applications.
The Future of Metal 3D Printing in the U.S. and Beyond
The sale of $22.4 million in metal 3D printers to U.S. customers is just the beginning of what is likely to be a major shift in manufacturing. As the technology continues to mature and more companies realize the benefits of additive manufacturing, we can expect to see an increasing number of industries adopt metal 3D printing as a core part of their manufacturing strategy.
In the coming years, metal 3D printing will likely become even more widespread as advancements in materials, printing speeds, and automation make the process more cost-effective and scalable. Furthermore, the integration of artificial intelligence (AI) and machine learning (ML) into the design and production process will enhance the capabilities of metal 3D printing, enabling even more precise and optimized parts.
Exentis’ success in the U.S. market represents a key moment in the ongoing evolution of additive manufacturing. With its innovative technology, strong customer base, and commitment to advancing the field, Exentis is well-positioned to remain at the forefront of the metal 3D printing revolution for years to come.