3D Printing in Automotive Manufacturing: Transforming the Production Line
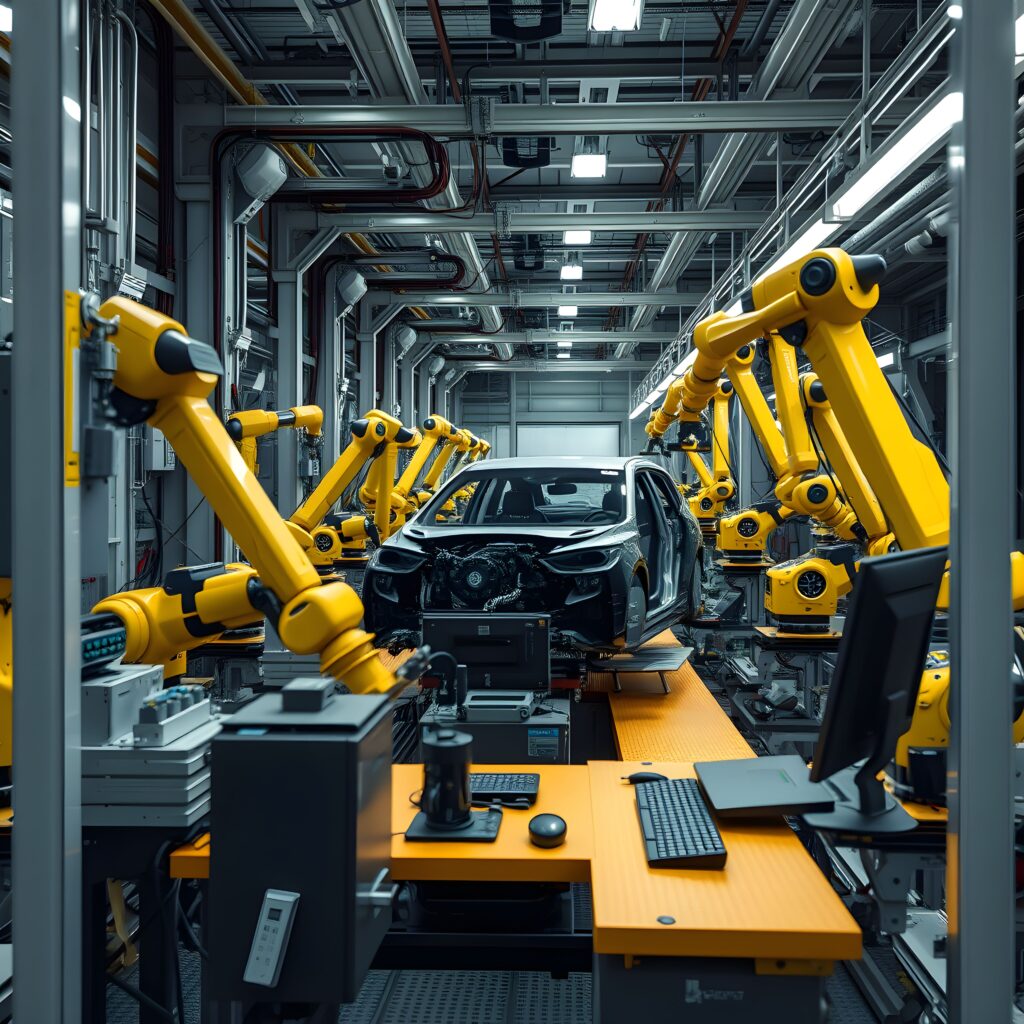
Introduction to 3D Printing in the Automotive Industry
The automotive industry is undergoing a significant transformation, with 3D printing playing a pivotal role in shaping the future of manufacturing. Known for its ability to produce complex parts with high precision, 3D printing is revolutionizing the way vehicles are designed and produced. From rapid prototyping to the creation of end-use parts, the applications of 3D printing in automotive manufacturing are vast and growing. As technology advances, automakers are discovering new ways to integrate this cutting-edge technique into their production lines, helping them reduce costs, speed up production, and improve design flexibility.
In its early stages, 3D printing was primarily used for prototyping, but today, it’s being used in production environments to manufacture real, functional parts. The technology has moved beyond just plastic components, with advancements in materials like metals, composites, and even ceramics allowing for the creation of stronger, more durable parts. These innovations are making it possible for manufacturers to meet increasing demands for customization, improved performance, and reduced environmental impact—all while maintaining high standards of quality and safety.
In this article, we will explore the various ways in which 3D printing is transforming the automotive industry, examining its benefits, challenges, and future potential.
The Basics of 3D Printing Technology in Automotive Manufacturing
3D printing, or additive manufacturing, involves creating three-dimensional objects by building up layers of material based on digital models. The process contrasts with traditional subtractive manufacturing, where material is cut away from a solid block. This fundamental difference allows for the creation of highly complex shapes and geometries that would be impossible or prohibitively expensive with conventional methods.
In automotive manufacturing, 3D printing is used in various stages, including design, prototyping, tooling, and even the final production of parts. The digital nature of 3D printing makes it highly adaptable, enabling designers to iterate quickly and efficiently. This has significant implications for the automotive industry, where innovation and speed are key competitive factors.
Several different 3D printing technologies are employed in automotive manufacturing, each with its own advantages and limitations. These include:
- Fused Deposition Modeling (FDM): A commonly used 3D printing technique that extrudes molten plastic through a heated nozzle to create layers.
- Selective Laser Sintering (SLS): A powder-based 3D printing technology that uses a laser to sinter particles of material into a solid structure.
- Stereolithography (SLA): A technique that uses ultraviolet light to cure liquid resin, layer by layer.
- Direct Metal Laser Sintering (DMLS): A process similar to SLS, but for metals, allowing manufacturers to produce functional metal parts directly from digital designs.
These technologies can create parts with varying degrees of strength, precision, and complexity, making them suitable for a wide range of applications in the automotive industry.
The Role of 3D Printing in Automotive Design and Prototyping
One of the most significant advantages of 3D printing in automotive manufacturing is its ability to accelerate the design process. Traditional methods of prototyping involved creating physical models using expensive materials and manual labor, often requiring multiple iterations. In contrast, 3D printing allows designers to quickly generate prototypes and test them in real-world conditions, which significantly reduces development time and costs.
With 3D printing, automakers can iterate on designs rapidly and make adjustments based on real-world testing. This flexibility is especially important in the automotive industry, where new models and technologies are constantly being developed. Designers can produce multiple versions of a part in a fraction of the time it would take using traditional methods. These prototypes can then be tested for form, fit, and function before any commitment is made to mass production.
In addition to speeding up the prototyping process, 3D printing enables greater design freedom. Designers are no longer restricted by the limitations of traditional manufacturing methods, which often require parts to be designed for ease of production. With 3D printing, parts can be optimized for performance rather than manufacturability. This opens up new possibilities for lightweight, complex, and highly functional designs that improve vehicle performance, efficiency, and aesthetics.
Applications of 3D Printing in Automotive Manufacturing
While prototyping remains one of the primary uses of 3D printing in the automotive industry, the technology is increasingly being used for end-use parts as well. Automakers are using 3D printing to create components that are used in the assembly of vehicles, such as brackets, connectors, and air ducts. These parts are often custom-designed to fit specific models or to meet specific performance requirements, making 3D printing an ideal solution.
One of the most significant benefits of using 3D printing for end-use parts is the ability to produce lightweight components. Lightweighting is a key focus for automakers, as reducing the weight of a vehicle can improve fuel efficiency, reduce emissions, and increase overall performance. 3D printing allows manufacturers to create parts that are both strong and lightweight, using materials such as carbon fiber and other composites that are difficult to manufacture using traditional methods.
Moreover, 3D printing can be used to create highly complex geometries that are not possible with conventional manufacturing techniques. This allows for the production of parts with integrated features, such as cooling channels or internal reinforcements, which would normally require multiple parts to be assembled together. By creating these features in a single, integrated part, automakers can reduce the number of components needed, streamline assembly processes, and improve overall part performance.
The Impact of 3D Printing on the Automotive Supply Chain
3D printing is also having a profound impact on the automotive supply chain. Traditionally, the production of automotive parts involves a complex network of suppliers and logistics systems, with parts being sourced from different regions and transported to various manufacturing facilities. This can be expensive and time-consuming, especially when dealing with low-volume or custom parts.
With 3D printing, automakers can produce parts on-demand, which eliminates the need for large inventories and complex supply chains. By printing parts locally or even on-site at the production facility, manufacturers can reduce shipping and storage costs, while also minimizing the risk of supply chain disruptions. This is particularly important in today’s global economy, where trade disruptions, such as those caused by the COVID-19 pandemic, have highlighted the vulnerabilities of traditional supply chains.
The on-demand nature of 3D printing also makes it an ideal solution for producing spare parts. In the past, automotive manufacturers had to keep large inventories of spare parts, which could be costly to store and maintain. With 3D printing, manufacturers can print spare parts as needed, reducing the need for excess inventory and allowing them to better manage their supply chains.
Cost Efficiency and 3D Printing in Automotive Manufacturing
Cost efficiency is one of the primary reasons automotive manufacturers are turning to 3D printing. Traditional manufacturing methods, such as injection molding and die casting, often require expensive tooling and molds. These molds can cost tens of thousands of dollars and take weeks or even months to produce. With 3D printing, there is no need for molds, which eliminates the initial costs and lead times associated with traditional manufacturing.
Prototyping is also much more affordable with 3D printing. Traditionally, creating a physical prototype required creating an entirely new part, often by hand, which could be both time-consuming and costly. With 3D printing, prototypes can be printed directly from digital files, allowing designers to quickly test and modify their designs. This makes the design process more efficient, reducing the time and cost associated with each iteration.
Additionally, 3D printing can help reduce the cost of producing low-volume or custom parts. Traditional manufacturing methods are often inefficient when it comes to small production runs, as the cost per part can be prohibitively high due to the cost of tooling and setup. With 3D printing, the cost per part remains consistent regardless of volume, making it an ideal solution for low-volume production or custom orders.
The Future of 3D Printing in Automotive Manufacturing
The future of 3D printing in automotive manufacturing is filled with potential. As the technology continues to evolve, we can expect to see even more innovative applications in the industry. One of the most exciting developments is the possibility of 3D printing being used for mass production. While 3D printing is currently primarily used for prototyping and low-volume production, the technology is advancing to the point where it could soon be used to produce high volumes of parts.
With the introduction of faster 3D printing methods and new materials, manufacturers are beginning to see the potential for 3D printing to compete with traditional manufacturing techniques in high-volume production. Companies are also experimenting with hybrid manufacturing methods, where 3D printing is combined with traditional techniques to optimize the production process and reduce costs.
Moreover, as the demand for electric and autonomous vehicles grows, 3D printing is expected to play a critical role in meeting these new challenges. The custom, lightweight, and high-performance parts that 3D printing can produce are perfectly suited to the needs of electric vehicles (EVs) and autonomous vehicles (AVs), which require specialized components for optimal performance and efficiency.
The Transformative Impact of 3D Printing in Automotive Manufacturing
In conclusion, 3D printing is transforming the automotive manufacturing industry in profound ways. From speeding up prototyping and enabling design flexibility to reducing costs and improving supply chain efficiency, the technology is revolutionizing every aspect of vehicle production. As 3D printing continues to evolve, its impact on the automotive industry will only grow, enabling manufacturers to meet the challenges of a rapidly changing market while driving innovation and sustainability.
Automotive manufacturers who embrace 3D printing will be well-positioned to stay ahead of the competition, offering faster time-to-market, more customized vehicles, and a more efficient production process. The potential applications of 3D printing in the automotive industry are vast, and the possibilities are limitless.
As we look to the future, 3D printing will undoubtedly continue to shape the automotive industry, driving advancements in design, production, and performance. By adopting this transformative technology, manufacturers can unlock new opportunities for growth and innovation, leading the way in the next generation of vehicles.