Real-World Applications of 3D Printing: Case Studies and Insights
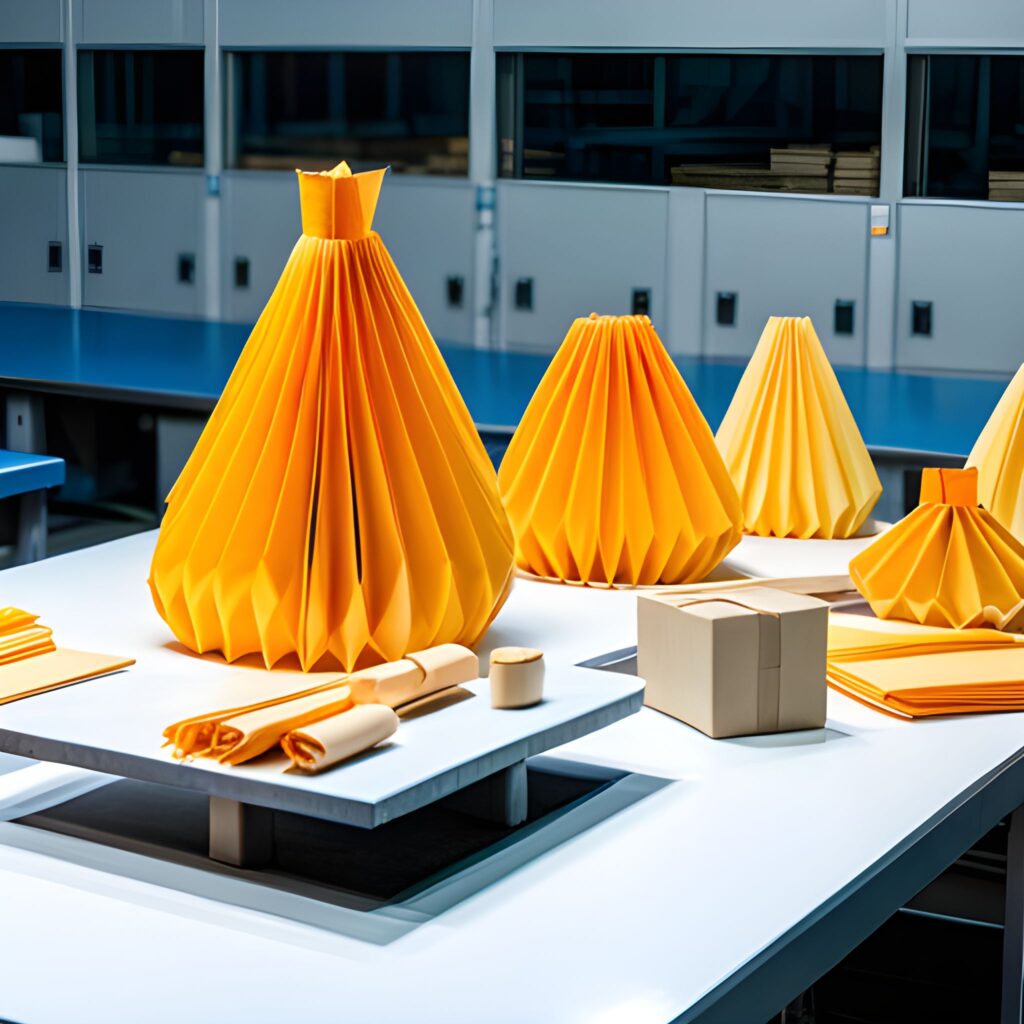
3D printing, also known as additive manufacturing, is no longer a futuristic concept but a transformative technology that is actively reshaping industries. This article explores how 3D printing is being applied across various sectors such as aerospace, healthcare, and automotive, revolutionizing production processes, improving efficiencies, and creating innovative solutions. Through real-world case studies, we’ll delve deeper into the steps, challenges, and outcomes of implementing 3D printing, illustrating its wide-reaching impact.
Case Study 1: Aerospace Industry – Optimizing Lightweight Aircraft Components
Background
The aerospace industry is one of the primary sectors that has embraced 3D printing due to its ability to create parts with complex geometries that are both lightweight and strong. The need for fuel-efficient, eco-friendly aircraft has driven aerospace engineers to explore additive manufacturing as an alternative to traditional machining methods. Conventional manufacturing methods, such as casting and machining, typically require a large amount of material to be removed, resulting in wastage and higher production costs. Additionally, traditional manufacturing has limitations when it comes to producing parts with intricate geometries.
In response, companies like Boeing, NASA, and Airbus have adopted 3D printing for producing aircraft components, significantly reducing the weight of key parts while maintaining strength. This optimization of lightweight components is particularly important in the aerospace industry, where even small reductions in weight can result in substantial improvements in fuel efficiency.
3D Printing Solution
3D printing allows aerospace engineers to design complex, lightweight components using topology optimization tools, which ensure that only the necessary material is used. Parts that would be difficult or impossible to create through traditional methods are now produced with ease using additive manufacturing. For example, Airbus and NASA have successfully used 3D printing to create brackets, air ducts, and structural components that are not only lighter but also more durable. The Selective Laser Sintering (SLS) and Direct Metal Laser Sintering (DMLS) technologies used in the aerospace sector involve melting metal powder layer by layer with a high-powered laser, resulting in a final product that is both strong and precise.
Detailed Process Steps
1. Design & Optimization
-
Aerospace engineers begin by analyzing aerodynamic and stress points in components. Using generative design software, engineers create optimized part designs that reduce weight without compromising strength. The software applies advanced algorithms to achieve the most efficient geometries, which might not be possible with traditional manufacturing methods.
-
For instance, engineers designing an aircraft bracket used topology optimization to remove excess material from the part while ensuring that the final design met all strength and performance criteria. The final design featured a honeycomb structure, which further reduced weight.
2. Slicing & Preparation
-
After designing the part, the model is converted into a 3D printable format, usually an STL file, using slicing software. The model is sliced into thin layers to prepare for the printing process, and engineers adjust layer thickness, print orientation, and support structures to optimize printing efficiency.
-
Support structures are particularly important in aerospace applications, as complex designs may need temporary structures to prevent deformation during the printing process.
3. Printing with Metal Powder Fusion
-
The printing process begins with metal powder (titanium or aluminum) being spread across the print bed. A high-powered laser then selectively fuses the powder layer by layer, creating the part’s shape as the material hardens.
-
Since the process is additive, only the material needed for the part is used, unlike traditional machining, which removes material from a larger block, resulting in significant waste.
4. Post-Processing & Heat Treatment
-
After printing, parts undergo post-processing steps such as heat treatment to remove internal stresses. This is crucial for ensuring the durability and structural integrity of the final component.
-
Support structures are removed, and parts are subjected to precision milling to achieve tight tolerances, as required by aerospace regulations.
5. Quality Inspection & Testing
-
Rigorous testing is done to ensure that the printed part meets all aerospace standards. Techniques like X-ray imaging, ultrasonic testing, and mechanical stress testing are used to verify the part’s strength, durability, and quality.
-
Once the part passes all quality checks, it is ready to be incorporated into the final product, such as an aircraft engine or wing structure.
Results & Benefits
The implementation of 3D printing in the aerospace sector has brought about numerous benefits, including:
- 50% weight reduction of components like brackets.
- Significant fuel efficiency improvements and lower carbon emissions.
- Reduced production times, with parts taking days instead of weeks to produce.
- Lower material wastage compared to traditional methods.
- Enhanced design flexibility, with the ability to create highly intricate geometries that were previously impossible or too expensive to manufacture.
By adopting 3D printing, aerospace companies are now able to create components that are both lighter and stronger, directly contributing to improved fuel efficiency and reduced operational costs. This case study showcases how additive manufacturing has become an integral tool in aerospace innovation and efficiency.
Case Study 2: Healthcare – Customized 3D-Printed Prosthetics
Background
The healthcare sector has also embraced 3D printing, particularly in the creation of customized prosthetics. Traditionally, prosthetic limbs were mass-produced, which often led to poorly fitting devices. Additionally, customization was limited, and prosthetics were expensive. As a result, patients frequently faced long wait times and discomfort due to poorly fitting limbs.
However, organizations like e-NABLE and Open Bionics have leveraged 3D printing technology to create affordable, customized prosthetic limbs that are tailored to each patient’s unique needs. Through 3D printing, these organizations have made significant strides in providing high-quality, personalized prosthetics at a fraction of the cost and production time of traditional prosthetics.
3D Printing Solution
To create 3D-printed prosthetics, engineers utilize CAD software and 3D scanning to design parts that fit precisely to the shape of the patient’s residual limb. This allows for a comfortable, snug fit while ensuring that the prosthetic is functional and durable. Materials such as PLA for rigid parts and TPU for flexible components are commonly used for different parts of the prosthetic.
Detailed Process Steps
1. 3D Scanning & Digital Design
-
A 3D scanner is used to capture the exact dimensions of the patient’s residual limb, ensuring a precise fit for the prosthetic. The scan is then converted into a digital model using CAD software like SolidWorks or Autodesk Fusion 360.
-
The prosthetic design includes functional features, such as mechanical fingers and adaptive grips for activities like grasping objects or typing. The design is then optimized for strength, flexibility, and comfort.
2. Slicing & Printing
-
The 3D model is then sliced into layers using slicing software, and the settings are configured for the chosen printing material, such as PLA or TPU.
-
The prosthetic is printed layer by layer using FDM (Fused Deposition Modeling) or SLA (Stereolithography) for fine detail. Each layer is fused together by the 3D printer, building the prosthetic from the ground up.
3. Multi-Material Printing
-
Multi-material printing allows for the creation of prosthetics that incorporate both rigid and flexible components. For instance, TPU is used for the joints and areas that require flexibility, while PLA is used for structural parts like the socket and casing.
-
This multi-material approach makes the prosthetic more comfortable and functional, mimicking natural limb movement.
4. Assembly & Finishing
-
Once the parts are printed, they are assembled, including the installation of components like actuators, screws, and straps for secure fitting.
-
Soft linings are also added to ensure comfort for the patient during wear, and cosmetic finishes like coloring or personalization are often incorporated to make the prosthetic more aesthetically pleasing.
5. Fitting & Testing
-
After assembly, the prosthetic is fitted to the patient and tested for fit, grip strength, and comfort. Adjustments are made based on feedback to improve the fit and functionality.
-
Patients test the prosthetic in various environments to ensure that it provides sufficient mobility and support.
Results & Benefits
- Cost reductions of up to 75% compared to traditional prosthetics.
- Rapid production time of a few days instead of weeks.
- Customized, comfortable fits that are tailored to each individual’s anatomy.
- Improved mobility and quality of life for users, especially in low-income regions and developing countries.
The adoption of 3D printing in prosthetics has been a game-changer in the healthcare industry, making high-quality, personalized prosthetic limbs accessible to a wider audience. This case study underscores the potential of 3D printing to improve the quality of life for individuals with limb differences, particularly in underserved communities.
Case Study 3: Automotive – Rapid Prototyping for Electric Vehicles
Background
The automotive industry is another major sector where 3D printing has brought significant improvements in production speed and design flexibility. Electric vehicle (EV) manufacturers like Tesla and Ford have incorporated 3D printing into their design and production processes. Traditional prototyping methods, such as molding and casting, can be slow and expensive, especially when testing new and innovative designs. In contrast, 3D printing enables the rapid creation of functional prototypes that can be tested and refined quickly, reducing both time and cost.
3D Printing Solution
Using 3D printing, automotive manufacturers can rapidly prototype complex components, such as battery enclosures, cooling systems, and lightweight chassis parts, which are crucial for EV performance. This allows manufacturers to iterate quickly and make design adjustments without the need for expensive molds and tooling.
Detailed Process Steps
1. Concept Design
-
Engineers use CAD software to design innovative components for electric vehicles. For example, Tesla engineers may design a new battery cooling system that maximizes efficiency.
-
Generative design algorithms are used to create lightweight components that offer the desired performance characteristics while reducing material usage.
2. 3D Printing of Prototypes
- The designs are then translated into 3D printable models using slicing software. Parts are printed using FDM technology with ABS or PLA filaments, which offer durability and strength.
3. Functional Testing
- Printed parts undergo functional testing, which includes evaluating their performance in real-world driving conditions. This testing helps identify any issues with component design before mass production begins.
4. Quality Control
- After testing, parts are inspected for defects or weaknesses and revised if necessary. This feedback loop helps refine the designs to meet specific EV production standards.
Results & Benefits
- 80% faster prototyping cycles compared to traditional methods.
- Reduced prototyping costs due to the elimination of expensive molds.
- Increased innovation through rapid iteration of designs and testing.
The adoption of 3D printing in the automotive sector, particularly for electric vehicles, has significantly accelerated innovation and reduced production costs. This case study highlights how rapid prototyping is crucial in developing next-generation automotive technology, making 3D printing an invaluable tool for EV manufacturers.
Transforming Industries Through Innovation
3D printing is a game-changing technology that is impacting multiple industries, from aerospace to healthcare to automotive. By enabling rapid prototyping, customization, and sustainable production methods, 3D printing is setting the stage for future innovations across sectors. As technology continues to evolve, we can expect even more industries to adopt additive manufacturing to revolutionize traditional production methods, ultimately driving global innovation and efficiency.