How to Design and Print Your Own 3D Printed Musical Instrument
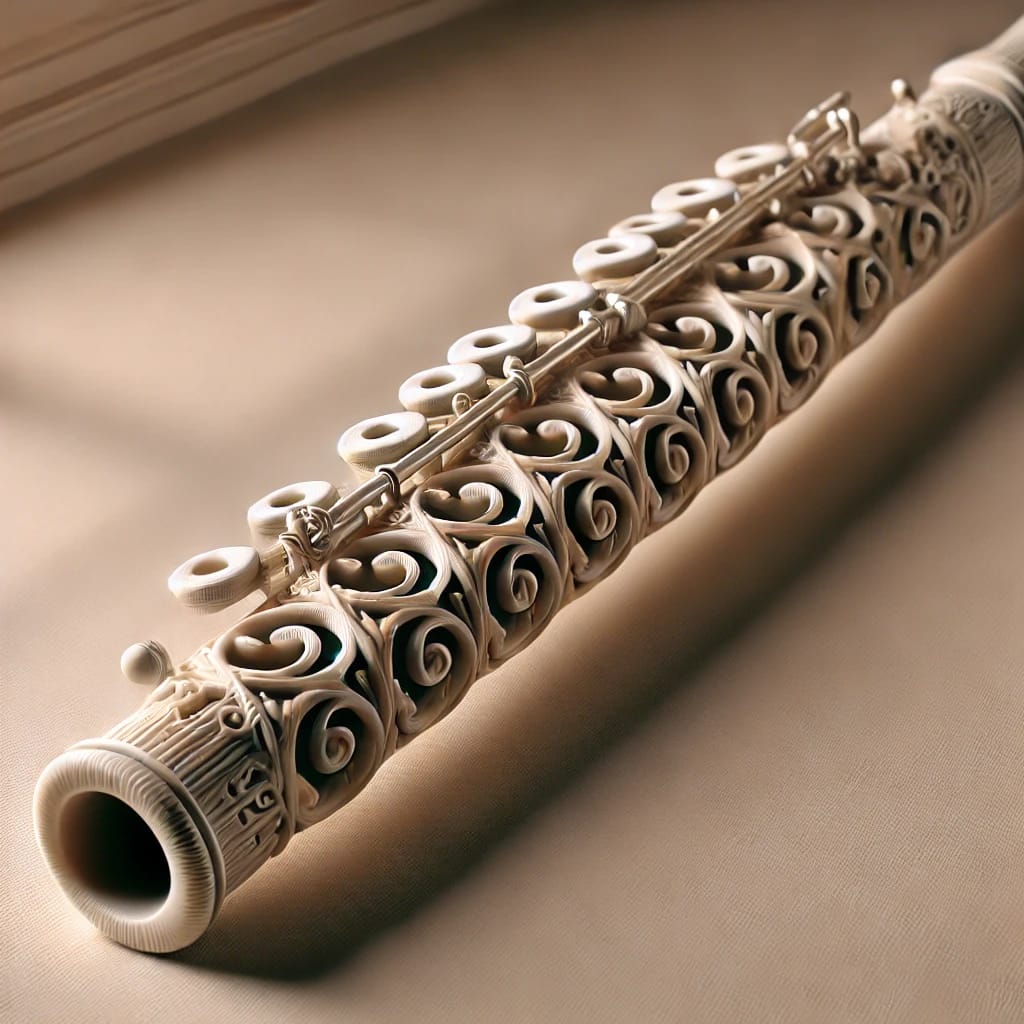
Learn how to design and create your own 3D printed musical instrument with this step-by-step guide. From software selection to printing techniques, craft the perfect instrument.
Design and Print Your Own 3D Printed Musical Instrument
Designing and printing your own 3D musical instrument can be a rewarding project that allows you to customize your sound and style.
This guide will take you through the process, from selecting the right software and materials to finalizing your design for printing like we discussed in the previous article https://master3dp.com/innovative-3d-pr…ndaries-of-sound/ .
1. Choosing the Right Software:
Your journey begins with selecting the right 3D modeling software. The software you choose should cater to your level of expertise and the complexity of the instrument you want to create.
Beginner-Friendly Options: If you’re new to 3D design, consider starting with user-friendly software like Tinkercad or Fusion 360. These programs offer intuitive interfaces and basic tools to get you started on your first design.
Advanced Software: For more complex designs, software like Blender or SolidWorks offers advanced modeling capabilities. These programs allow for intricate detailing and fine-tuning of your instrument’s design, giving you full control over every aspect of the geometry.
2. Designing Your Instrument:
Once you’ve selected your software, it’s time to design your instrument. This stage involves careful planning and creativity to ensure that the final product meets your expectations in both form and function.
Consider Ergonomics and Playability: When designing the instrument, think about how it will be played. The ergonomics of the instrument, such as the shape of a guitar neck or the placement of keys on a wind instrument, are crucial for playability. Make sure to test the design with prototypes if possible to refine the ergonomics.
Acoustic Design Elements: For instruments like wind or string instruments, the internal structure plays a significant role in sound production. Use your software to experiment with different shapes and internal geometries to influence the instrument’s tonal qualities. Consider consulting with an acoustic engineer if you’re aiming for a specific sound profile.
3. Selecting Materials:
The choice of material can greatly affect both the appearance and sound of your instrument. It’s important to choose a material that suits the instrument type and desired acoustic properties.
Material Options: Common 3D printing materials include PLA, ABS, and resin. PLA is a good choice for beginners due to its ease of use and versatility. For instruments requiring more durability, such as those that will be played frequently, ABS or nylon may be more suitable.
Experimenting with Composites: If you’re looking to achieve specific acoustic properties, consider using composite filaments like wood or metal-infused PLA. These materials can mimic the sound characteristics of traditional wood or metal instruments.
4. Printing and Post-Processing:
After finalizing your design, it’s time to print the instrument. This stage involves preparing your 3D printer and post-processing the printed parts to achieve the desired finish.
Printer Settings: Ensure that your printer is calibrated correctly and use appropriate settings for the chosen material. For example, slower print speeds and higher resolution settings can improve the surface quality of the final print.
Post-Processing Techniques: Once printed, you may need to perform some post-processing steps, such as sanding, painting, or assembling different parts of the instrument. For string instruments, you might need to add hardware like tuning pegs or a bridge.
Designing and printing your own 3D musical instrument is a fascinating process that allows for endless creativity and customization. By carefully planning your design, choosing the right materials, and fine-tuning the acoustic properties, you can create a unique instrument that not only looks amazing but sounds incredible too.