Smart Materials: 3D Printing with Color-Changing CLCEs
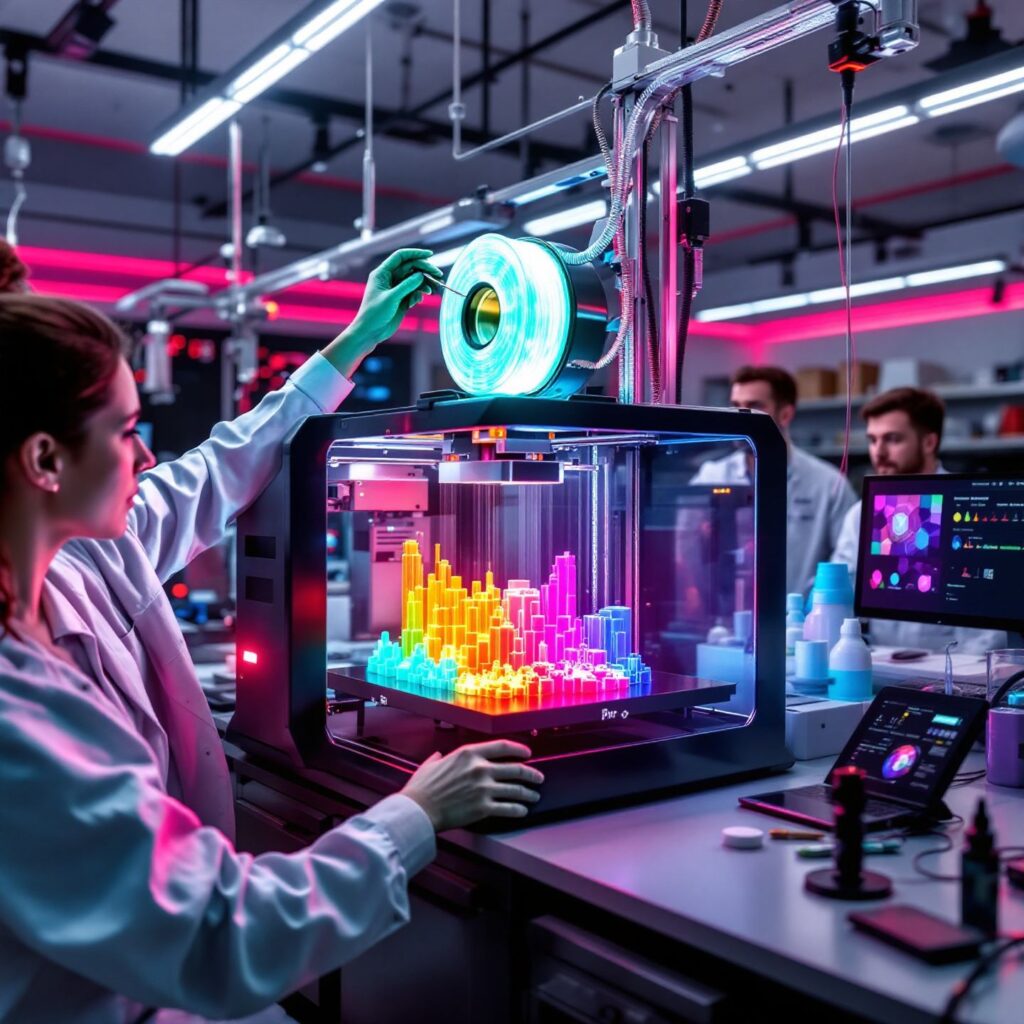
A New Era in Materials Science
In recent years, the realm of 3D printing has transformed from simple plastic modeling to advanced, multi-functional material fabrication. While traditional polymers still dominate consumer-level printers, the integration of smart materials into additive manufacturing is pushing the boundaries of what’s possible. One standout in this new wave of innovation is the use of cholesteric liquid crystal elastomers (CLCEs).
CLCEs are capable of changing color based on mechanical stress or temperature changes. Unlike basic filaments used in early 3D printing, CLCEs introduce intelligence into materials by responding dynamically to environmental stimuli. This color shift is not merely aesthetic; it provides real-time visual feedback on stress, strain, and temperature—traits valuable in wearable tech, robotics, and aerospace.
The concept of responsive or “smart” materials is not new, but the ability to manufacture them with precision using 3D printing is a breakthrough. Previously, smart materials often required complex chemical treatments or limited manufacturing environments. Now, thanks to direct ink writing (DIW) and multi-material extrusion techniques, researchers are creating responsive, functional components directly from 3D models.
Moreover, this innovation is not only technical—it is strategic. Industries are turning toward sustainability, flexibility, and precision in their manufacturing processes. Smart 3D-printed CLCEs align with these goals by reducing waste, improving customization, and enhancing product longevity through self-monitoring capabilities.
In this article, we will explore the structure and science of CLCEs, detail the 3D printing techniques used to produce them, examine their key applications, and consider the future implications of this technology in global industries. Each section will provide an in-depth, step-by-step analysis to ensure clarity for readers from all backgrounds.
Understanding CLCEs: Cholesteric Liquid Crystal Elastomers
To understand why CLCEs are so revolutionary, one must first break down their composition. Cholesteric liquid crystals are a subclass of liquid crystals that exhibit a helicoidal molecular structure, reflecting specific wavelengths of light. This molecular alignment causes them to display brilliant colors, which change when their structure is altered by external forces.
These crystals are embedded within a flexible elastomer, giving the material both shape-memory and color-shifting properties. The resulting hybrid, a CLCE, behaves like rubber but can shift hues in reaction to mechanical stretching or compression. This color-changing behavior is based on Bragg reflection, where light waves interfere constructively or destructively depending on the pitch of the molecular helix.
When a CLCE is stretched, the pitch of the helix increases, which causes the material to reflect shorter wavelengths (shifting toward the blue end of the spectrum). Conversely, compression shifts the reflected color toward red. This transformation is not just visually striking; it serves as a real-time diagnostic tool in materials engineering and healthcare.
Because CLCEs are highly sensitive, they must be handled with care during fabrication. This sensitivity posed a major challenge in integrating them with traditional 3D printing techniques. Standard methods involving high temperatures or harsh solvents would degrade their structure. However, innovations in low-temperature printing and customized ink formulations have solved this.
Recent studies, including one published in Nature Materials (April 2025), have shown that pre-aligned cholesteric mesogens can be integrated into printable inks. These inks retain their reflective and elastic properties after curing, making them suitable for direct patterning into complex geometries.
Furthermore, the elastic matrix within CLCEs provides durability and flexibility. Unlike brittle photonic materials, CLCEs return to their original shape and color once the stress is removed. This reversibility makes them ideal for repeated use in strain sensors, wearables, and even optical camouflage materials.
As industries push toward more adaptive and intelligent designs, the versatility of CLCEs offers a powerful toolkit for creating materials that not only endure but communicate their condition.
How CLCEs Are 3D Printed: Step-by-Step Manufacturing Process
Printing CLCEs requires a specialized approach that differs significantly from traditional filament-based FDM printers. The process primarily utilizes Direct Ink Writing (DIW), a method where viscoelastic inks are extruded through a nozzle to form three-dimensional structures.
Step 1: Formulating the CLCE Ink
The process begins with the preparation of a printable CLCE ink. This involves mixing cholesteric mesogens with a polymeric elastomer base. Precise ratios are critical, as they determine the optical and mechanical properties of the final product. A photoinitiator is often added to allow UV curing after printing.
Step 2: Temperature and Humidity Control
CLCE inks are sensitive to environmental conditions. Therefore, the printing environment must be carefully controlled, often within a sealed chamber that regulates temperature (typically below 80°C) and humidity. This ensures the helicoidal structure remains intact during deposition.
Step 3: Nozzle Alignment and Patterning
To achieve the correct optical effect, the printing nozzle must align the liquid crystal domains during extrusion. This alignment is achieved using shear forces, induced by precisely controlling the extrusion rate and nozzle speed. The material is printed layer by layer, with each layer curing either photochemically or thermally.
Step 4: Post-Processing
After printing, the structure undergoes curing, usually via UV light, to lock in the desired alignment. In some cases, thermal annealing may also be used to improve the order of the crystal domains and enhance color vibrancy.
Step 5: Testing and Calibration
The finished structure is tested under mechanical stress to confirm its responsive behavior. Researchers measure color shifts using spectrophotometers and correlate them with specific strain values, allowing the material to be calibrated as a sensor.
Through this detailed printing pipeline, engineers can create components that are not only strong and flexible but also communicate their physical state through color.
Applications: Where CLCE-Based 3D Printing Is Making an Impact
The real-world uses for 3D-printed CLCEs are expanding rapidly, with applications spanning across various industries.
1. Wearable Technology
One of the most promising uses is in smart clothing. Fabric made with embedded CLCE fibers can change color to indicate muscle strain or joint movement. Athletes and physical therapists can benefit from real-time, color-coded feedback during training or rehabilitation.
2. Aerospace and Automotive Sensors
In high-stress environments like space missions or car manufacturing, CLCEs can serve as passive stress indicators. Rather than relying on electronic sensors, components can visually indicate where wear or damage is occurring, simplifying maintenance and inspections.
3. Biomedical Devices
CLCEs are also being studied for use in implants and prosthetics, where color changes can indicate internal stress, potential damage, or even pressure sores. Their biocompatibility is currently under clinical testing in Europe and India.
4. Soft Robotics
Because they are elastic and responsive, CLCEs are ideal for use in soft robotic skins. These materials allow robots to “feel” their surroundings and provide visual cues when overstressed, contributing to safer human-robot interaction.
5. Smart Packaging and Labels
In logistics, CLCEs can serve as tamper-proof indicators. Packages can change color if exposed to damaging forces during transit, offering immediate visual feedback on whether the contents are safe.
6. Consumer Electronics
CLCEs are being integrated into flexible screens and ambient-responsive cases that shift color with touch or temperature, offering new avenues in design and personalization.
Each application benefits from the durability, reversibility, and responsiveness of CLCE materials. Moreover, since these structures are 3D printed, they can be tailored for specific geometries and user needs, making them highly customizable.
Challenges and Limitations: What Still Needs to Be Solved
Despite the promising future, several challenges must be addressed before CLCEs become mainstream in manufacturing.
1. Cost and Scalability
Current production costs for CLCE inks remain high due to the complexity of synthesis. While pilot programs are underway, commercial-scale deployment is still under development.
2. Long-Term Stability
Though reversible, CLCEs may degrade over time due to UV exposure or repeated stress. Research is ongoing to enhance their durability without sacrificing responsiveness.
3. Printing Resolution
Achieving high-resolution alignment of cholesteric domains is technically demanding. Errors during extrusion can result in color inconsistency or optical artifacts.
4. Regulatory Approvals
Especially in biomedical and aerospace applications, CLCEs must pass rigorous safety and performance standards. Ongoing testing is necessary before widespread use is permitted.
Despite these hurdles, research in 2024–2025 has shown remarkable progress, with institutions like MIT, ETH Zurich, and AIIMS India leading the charge in innovation.
The Road Ahead: What the Future Holds for CLCEs and Smart Printing
The path forward for CLCE technology in 3D printing is both exciting and expansive.
New research is focusing on multi-stimuli-responsive CLCEs, capable of responding not just to mechanical force but also to electric fields, magnetic fields, and chemical exposure. This evolution could lead to fully autonomous sensing systems in critical infrastructure.
Efforts are also underway to integrate CLCE printing into consumer-grade printers, making it more accessible for DIY creators and educators. This democratization could inspire a new generation of innovators.
The merging of AI-based design tools with CLCE fabrication is another promising trend. Algorithms can simulate stress patterns and predict color shifts before printing, allowing for smarter design optimization.
Lastly, as climate challenges increase, the push for sustainable, self-monitoring materials will likely accelerate. CLCEs, with their ability to function without electronic components, offer a low-energy, eco-friendly solution to many modern challenges.
Smart materials like CLCEs are redefining what it means to “print” something. No longer limited to static, inert objects, 3D printing is moving into a realm where materials respond, adapt, and communicate. With continued innovation, collaboration, and testing, the future of 3D printing could very well be alive with color, motion, and intelligence.
Feel free to check out our other website at http://master3dp.com/ where you can learn to 3D print anything needed for a project.